Panhard Cylinder Liner Rebore Update 6
28/10/12 15:08 Filed in: Panhard Piston | Whatton
Yesterday, I machined a couple of test liners from an early Dyna engine, and after inspecting them, I decided I would do a test fit in the aluminium cylinder to see what difference there was in the bore diameter due to the interference fit.
After warming up the bare cylinder with the big propane torch, I placed the cylinder in, and rotated it into the correct position (these liners have cut outs for the crankshaft webs).
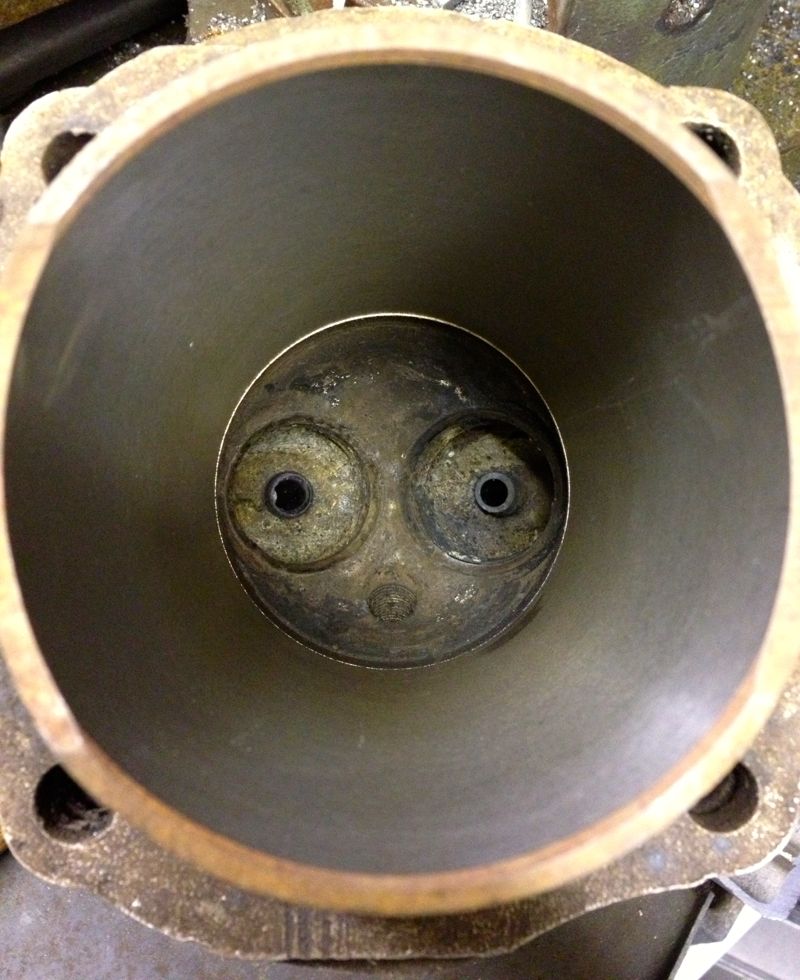
Once it was cool, I decided to take a remeasure, and see how the dimensions compared.
I started off with this measurement from yesterday, but when the sleeve or liner was placed in the cylinder I got the measurement in the second picture below.
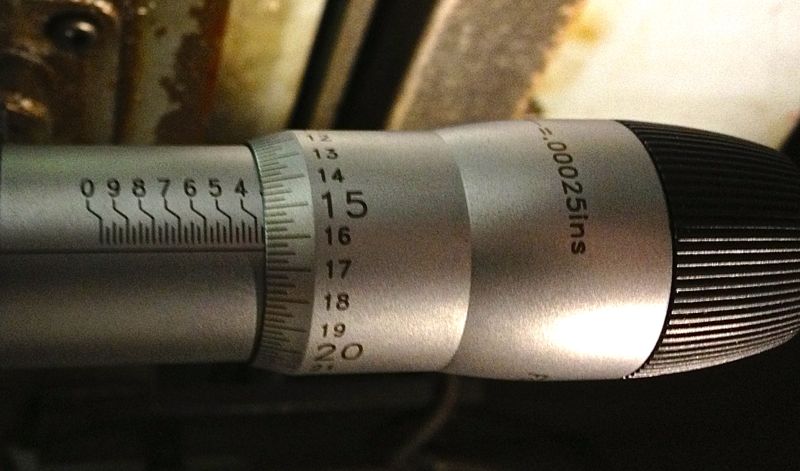
To be honest, I thought the cylinder was larger than this picture above when I measured it this morning at around the “17.25” mark, which represents 3.36725”, but for some reason I have mislaid the picture.

Either way this represents a 0.003”-0,004” squeeze depending what picture I look at, and as I moved the micrometer out of the cylinder and took further measurements along the way, I got the following…
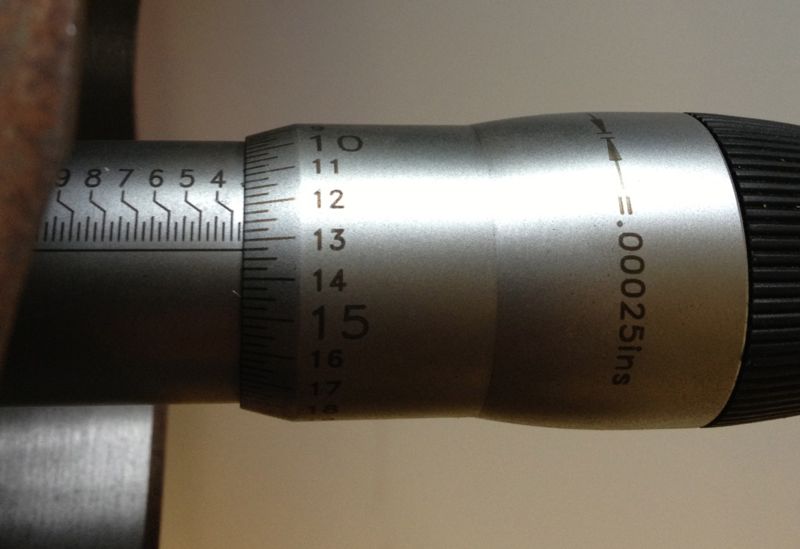
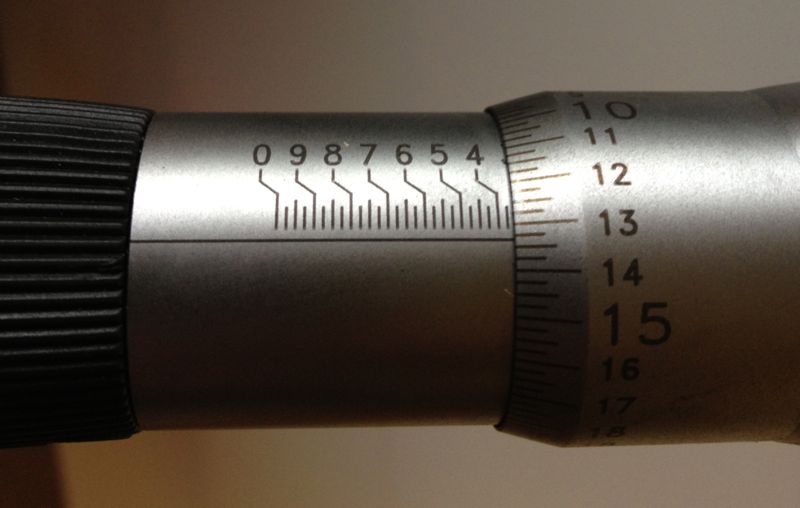
As the liner left the grip of the cylinder the sleeve opened up, as shown below.
At the skirt perimeter it measured even bigger still at 3.36775”, but this isn’t a huge deal, but it is interesting that a parallel bored liner deflects this much.
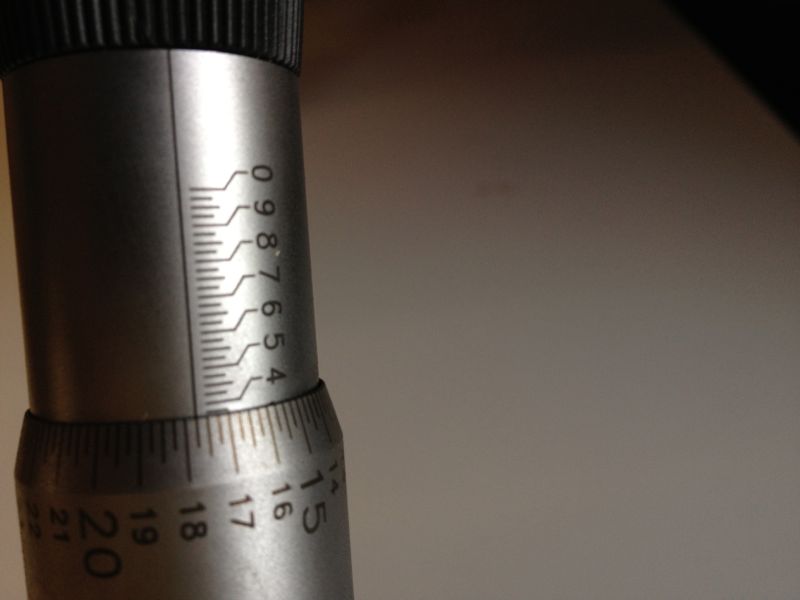
So yet again, we have the issue of an interference fit and the folklore surrounding a tapered bore. The last liner I machined using the Whatton actually produced a tapered bore, and the taper runs in the right direction too, because it is smallest at the hottest end.
I now know how to achieve this, and after playing with the Whatton some more, i have ascertained why it is happening. Anyway, it is an accidental product of my curiosity, and what relevance it has on real world engines is unproven. I will explore this option when the engine dyno test facility is up and running, to see if it is beneficial.
On the subject of taper, here are two pictures of a bare piston in the cylinder liner, but turned through 90º. Notice the difference in the resting height, this is due to the ovality of the piston, and the bore being smaller than the pistons nominal diameter of 85.4mm or 3.3622”
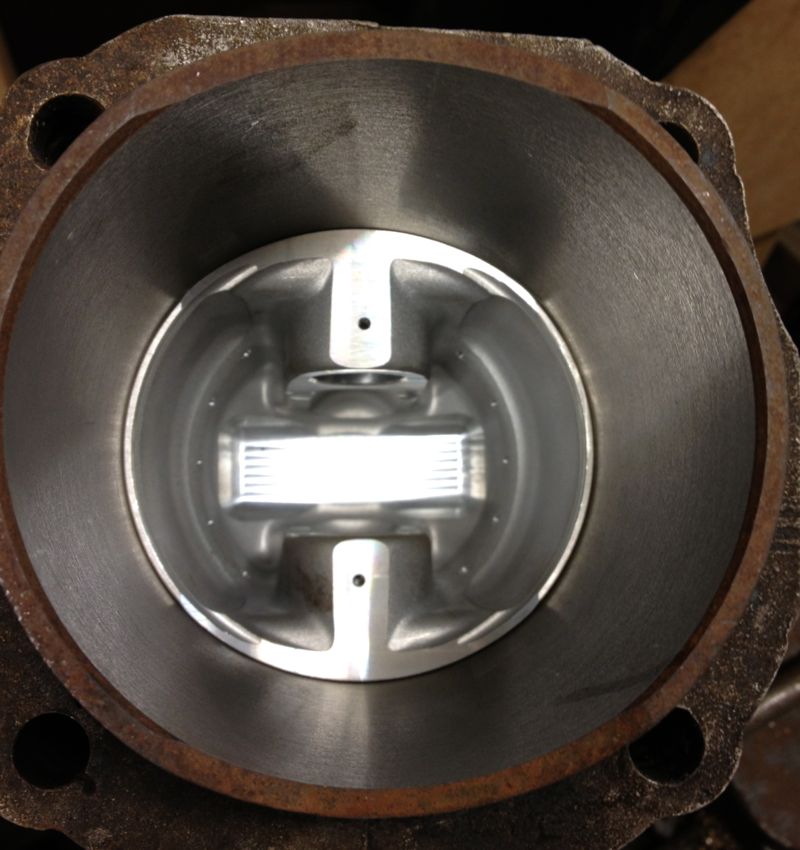
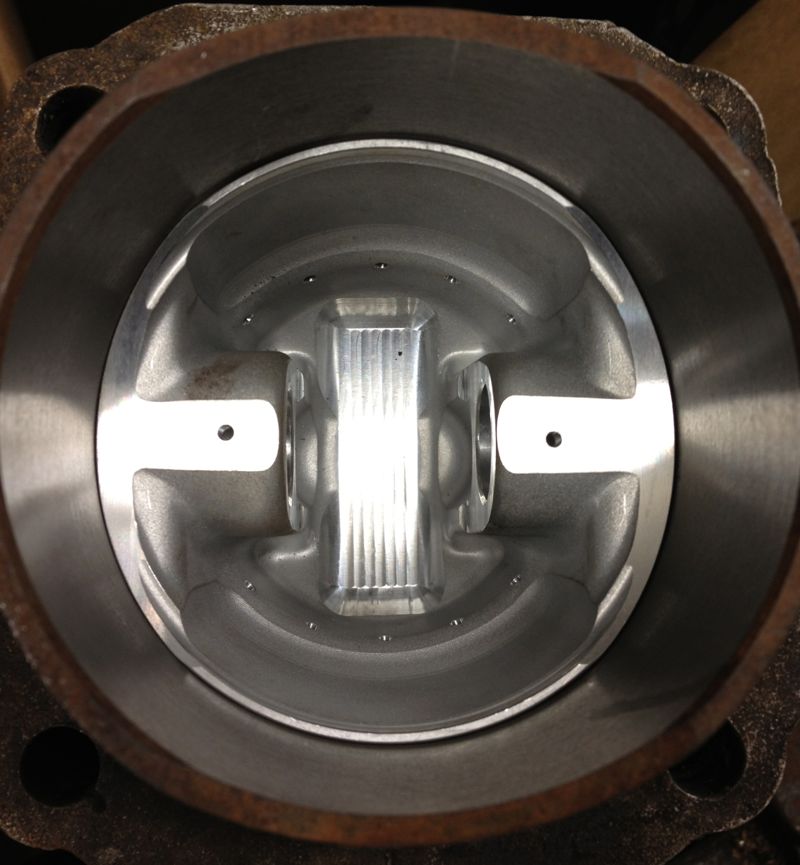
Obviously with the interference fit, the liner is slightly smaller than the expected size, as it reads 3.36320” diameter over it’s running surface, and it’s recommended value of 85.5mm equates to 3.36614”, so it’s 0.003“ undersize, or operating on a 0.001” piston to bore clearance. Actually, in modern 2 valve race engines, with very light pistons and a better spec liner material, I have seen 0.0015” clearance on an air-cooled V twin.
It did seize, because of a fuelling error, which caused it to run too hot and the piston grabbed in the bore. It was a real nice engine, but I cannot say how many horses it had at the wheel, but it was over 10% of its capacity in cubic centimetres measured in DIN RWHP, and all from a two valve head.
After warming up the bare cylinder with the big propane torch, I placed the cylinder in, and rotated it into the correct position (these liners have cut outs for the crankshaft webs).
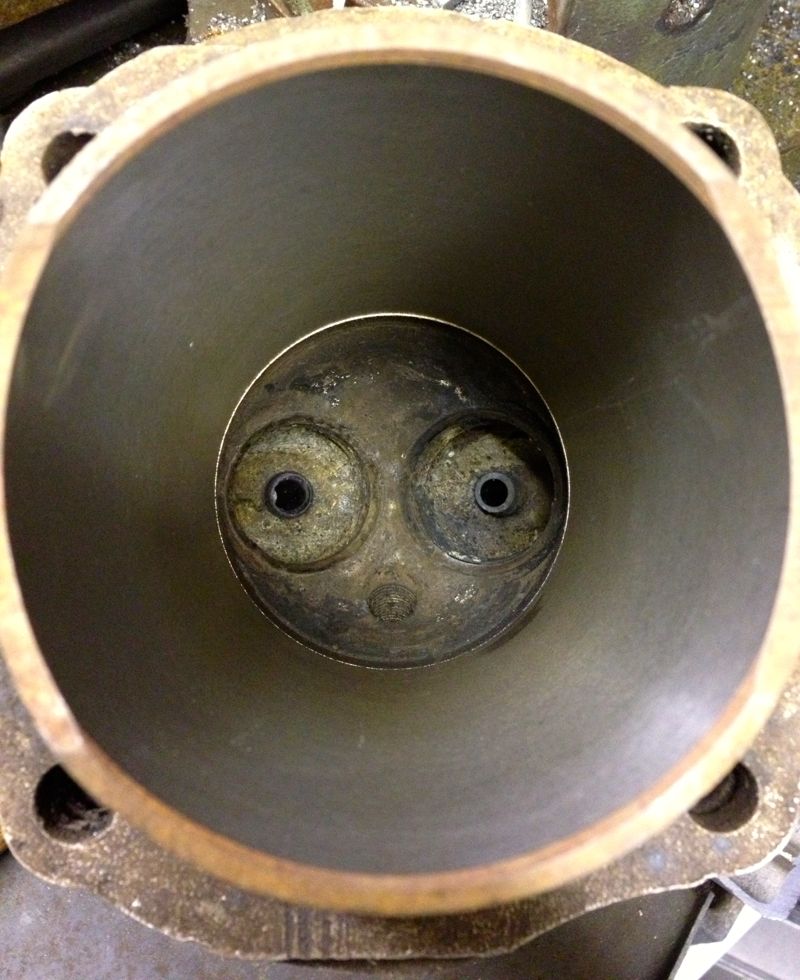
Once it was cool, I decided to take a remeasure, and see how the dimensions compared.
I started off with this measurement from yesterday, but when the sleeve or liner was placed in the cylinder I got the measurement in the second picture below.
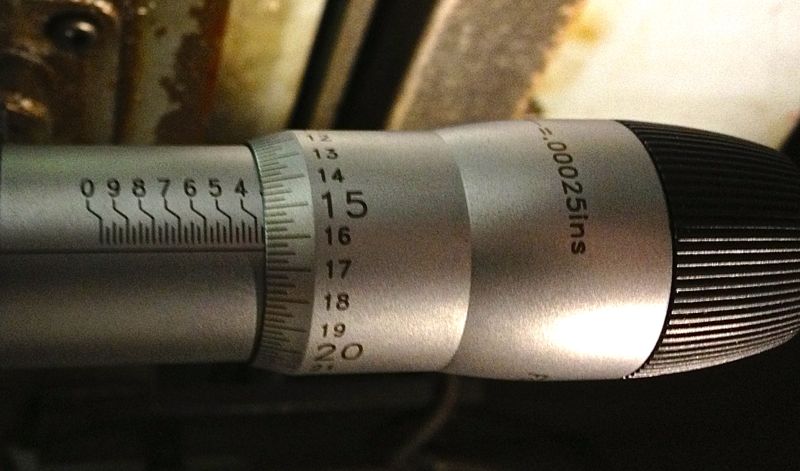
To be honest, I thought the cylinder was larger than this picture above when I measured it this morning at around the “17.25” mark, which represents 3.36725”, but for some reason I have mislaid the picture.

Either way this represents a 0.003”-0,004” squeeze depending what picture I look at, and as I moved the micrometer out of the cylinder and took further measurements along the way, I got the following…
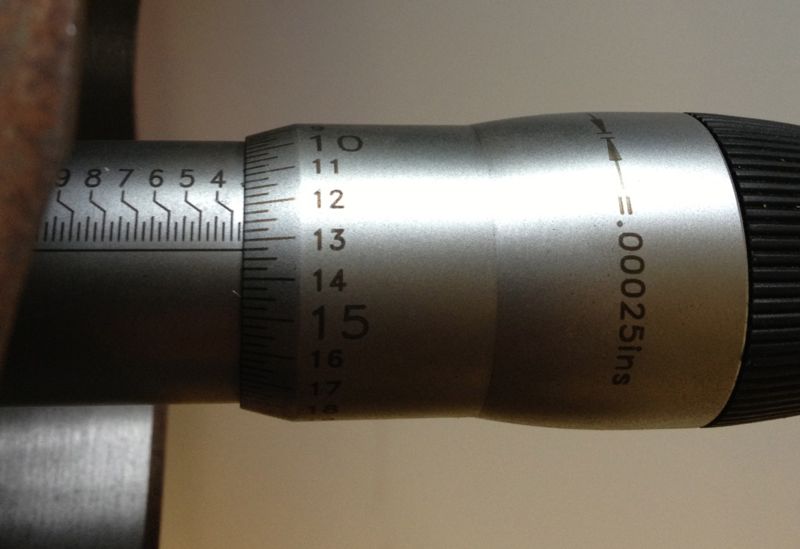
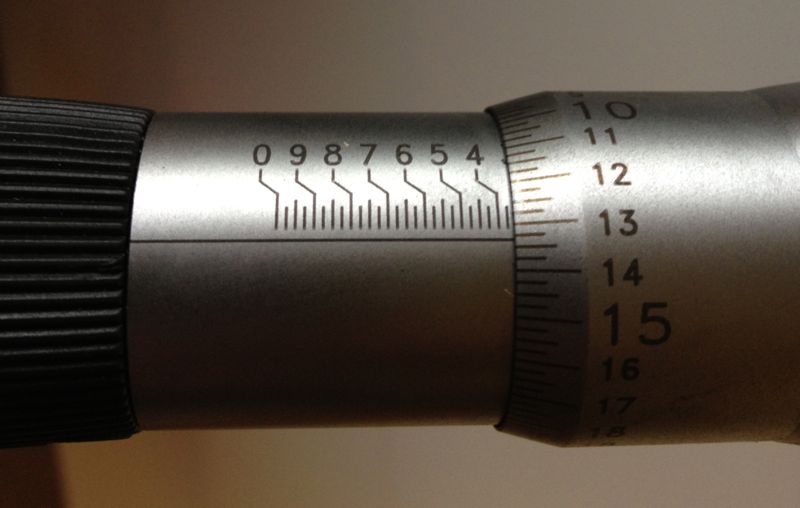
As the liner left the grip of the cylinder the sleeve opened up, as shown below.
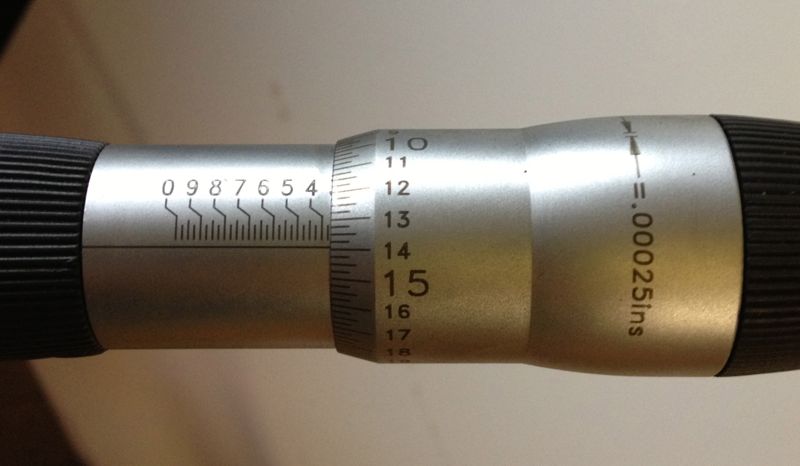
At the skirt perimeter it measured even bigger still at 3.36775”, but this isn’t a huge deal, but it is interesting that a parallel bored liner deflects this much.
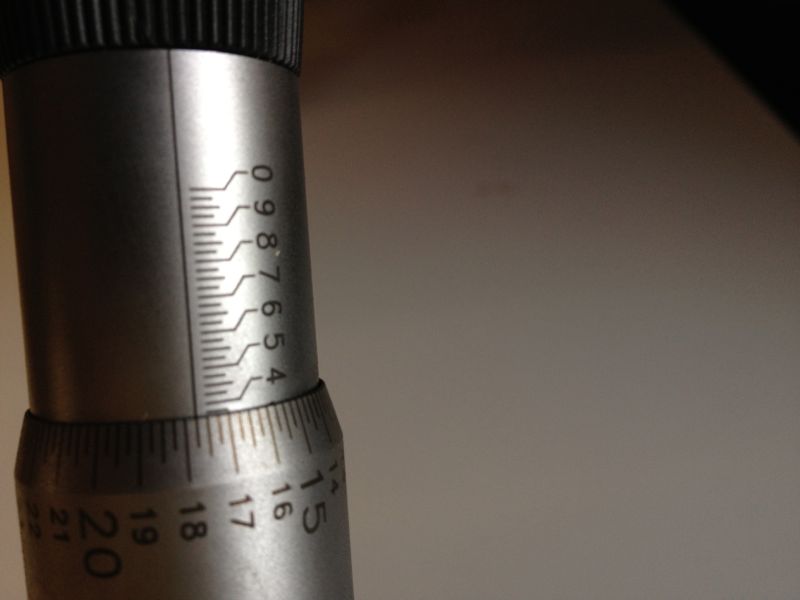
So yet again, we have the issue of an interference fit and the folklore surrounding a tapered bore. The last liner I machined using the Whatton actually produced a tapered bore, and the taper runs in the right direction too, because it is smallest at the hottest end.
I now know how to achieve this, and after playing with the Whatton some more, i have ascertained why it is happening. Anyway, it is an accidental product of my curiosity, and what relevance it has on real world engines is unproven. I will explore this option when the engine dyno test facility is up and running, to see if it is beneficial.
On the subject of taper, here are two pictures of a bare piston in the cylinder liner, but turned through 90º. Notice the difference in the resting height, this is due to the ovality of the piston, and the bore being smaller than the pistons nominal diameter of 85.4mm or 3.3622”
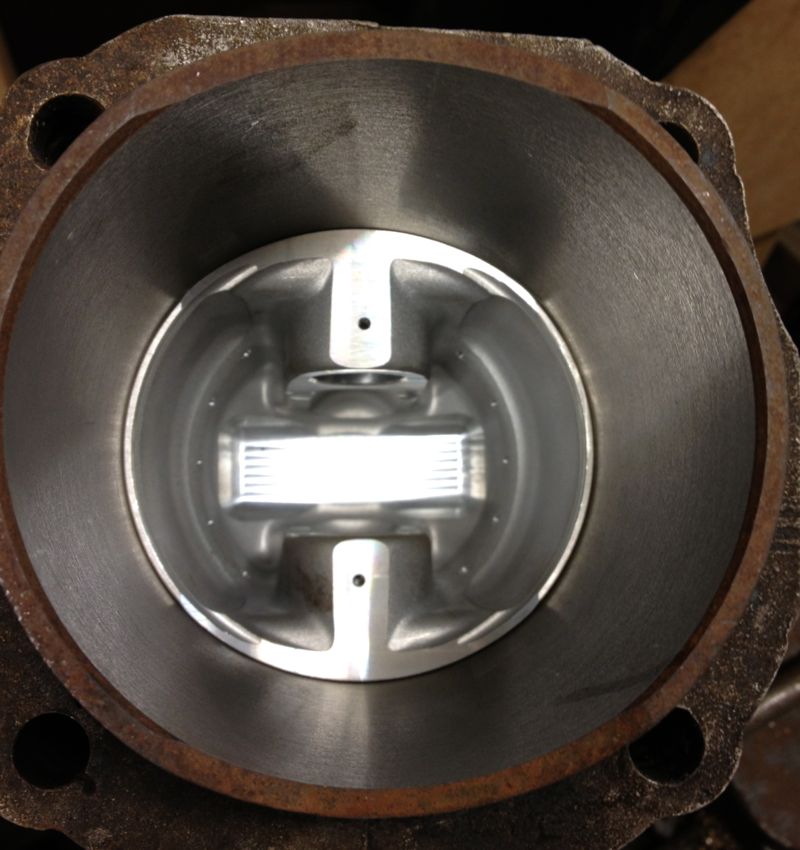
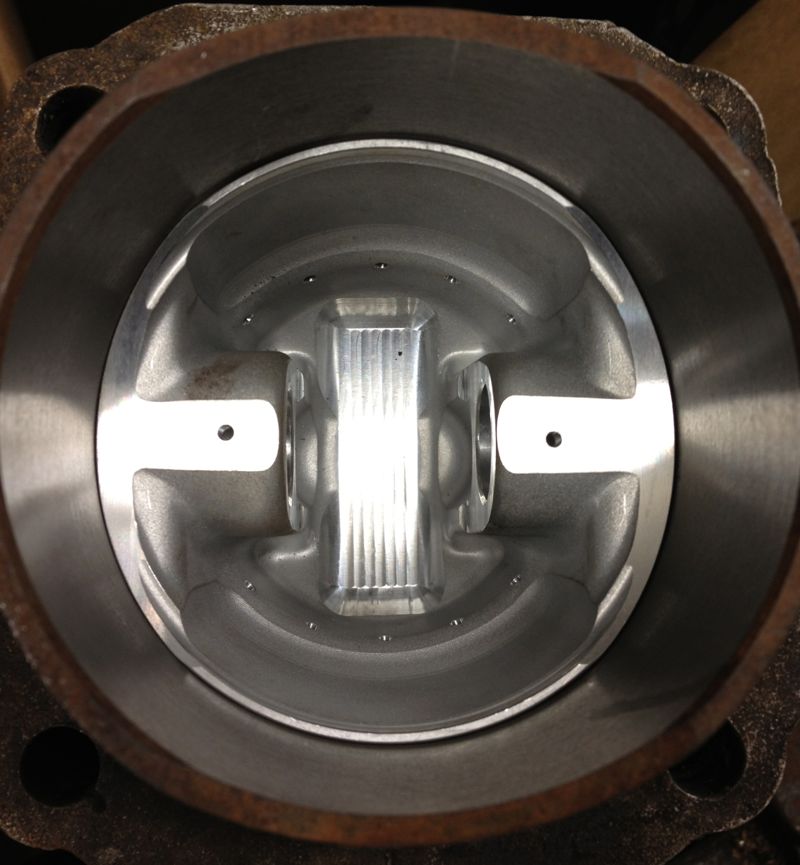
Obviously with the interference fit, the liner is slightly smaller than the expected size, as it reads 3.36320” diameter over it’s running surface, and it’s recommended value of 85.5mm equates to 3.36614”, so it’s 0.003“ undersize, or operating on a 0.001” piston to bore clearance. Actually, in modern 2 valve race engines, with very light pistons and a better spec liner material, I have seen 0.0015” clearance on an air-cooled V twin.
It did seize, because of a fuelling error, which caused it to run too hot and the piston grabbed in the bore. It was a real nice engine, but I cannot say how many horses it had at the wheel, but it was over 10% of its capacity in cubic centimetres measured in DIN RWHP, and all from a two valve head.
blog comments powered by Disqus