Panhard Twin Plugging Cylinders 1
29/03/13 21:32 Filed in: Panhard Engine
Twin plugging is adding another spark plug to each cylinder, so that each cylinder has two plugs. This is beneficial in a domed piston , domed combustion chamber environment, because the flame front can be chopped short by the lopsided combustion processes. To make sure this non ideal combustion is completed, it’s usual to run plenty of ignition advance, and as the rpm goes up this advance figure rises. High advance exposes the cylinder components to a longer heat exposure, so the engine runs hotter too.
If you look at the Panhard combustion chambers you can see the spark plug angle is less than ideal, and there is evidence of electrode shielding too, so Brian’s engine will have surface
discharge spark plugs, which are at a disadvantage at low speed, & lean mixtures, so fitting an extra spark plug will negate some of this.
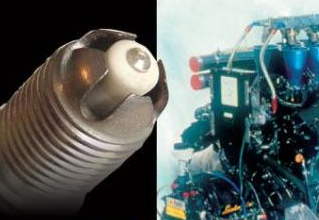
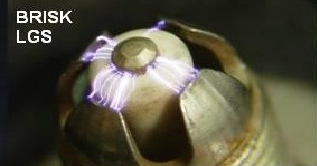
How do you twin plug a cylinder?
You’ll need access to a milling machine ideally, worst case a pillar drill and a Dremel. Sequence of events are,
1. Establish existing spark plug position.
2. rotate cylinder 180º.
3. Drill, tap & mill the spark plug recess.
4. Mill the fins to allow for spanner access.
Here is the start of my jig, which was some reused components from the crankshaft rig, and the honing clamp parts.
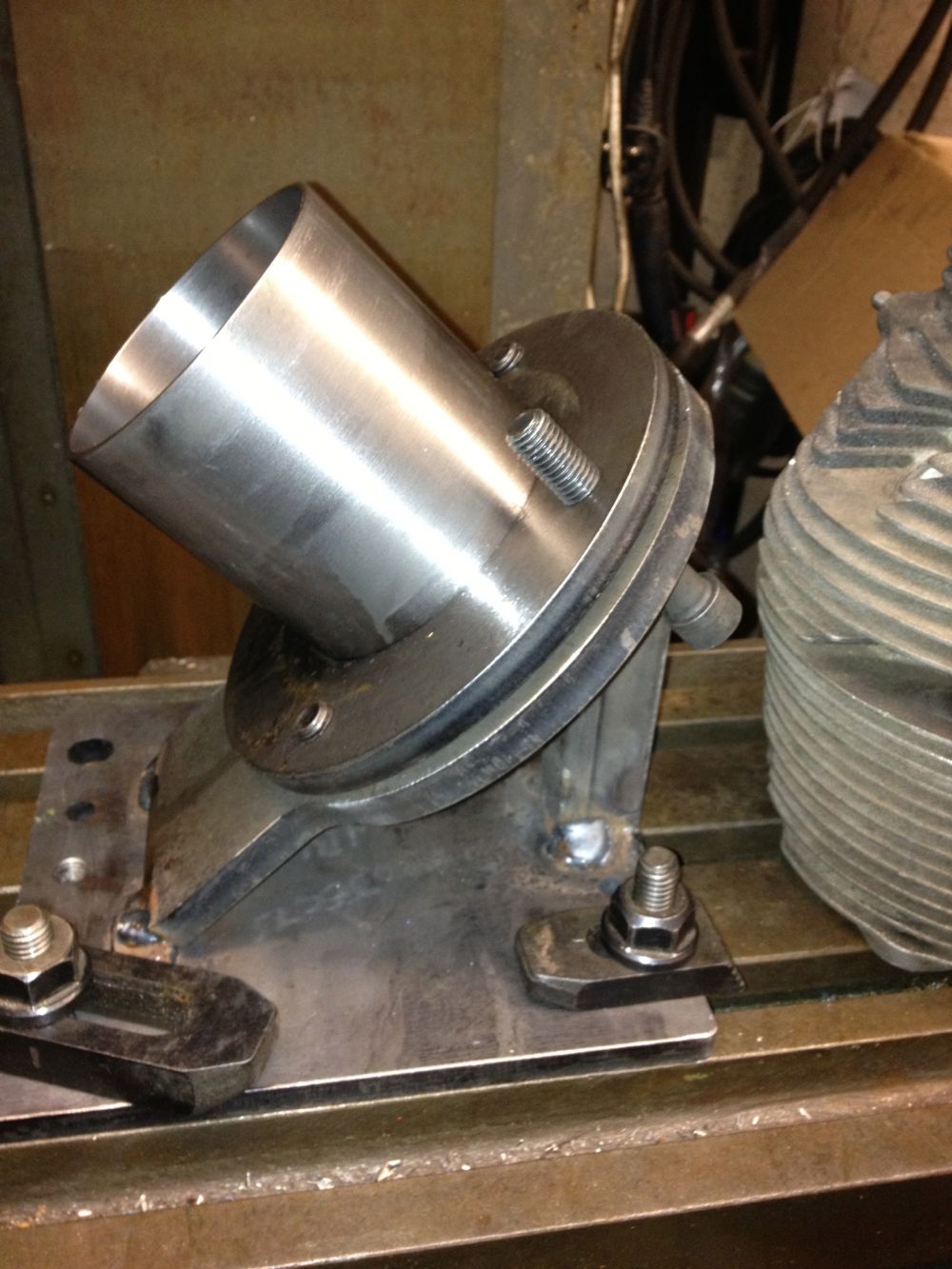
Checking everything is vertical and aligned
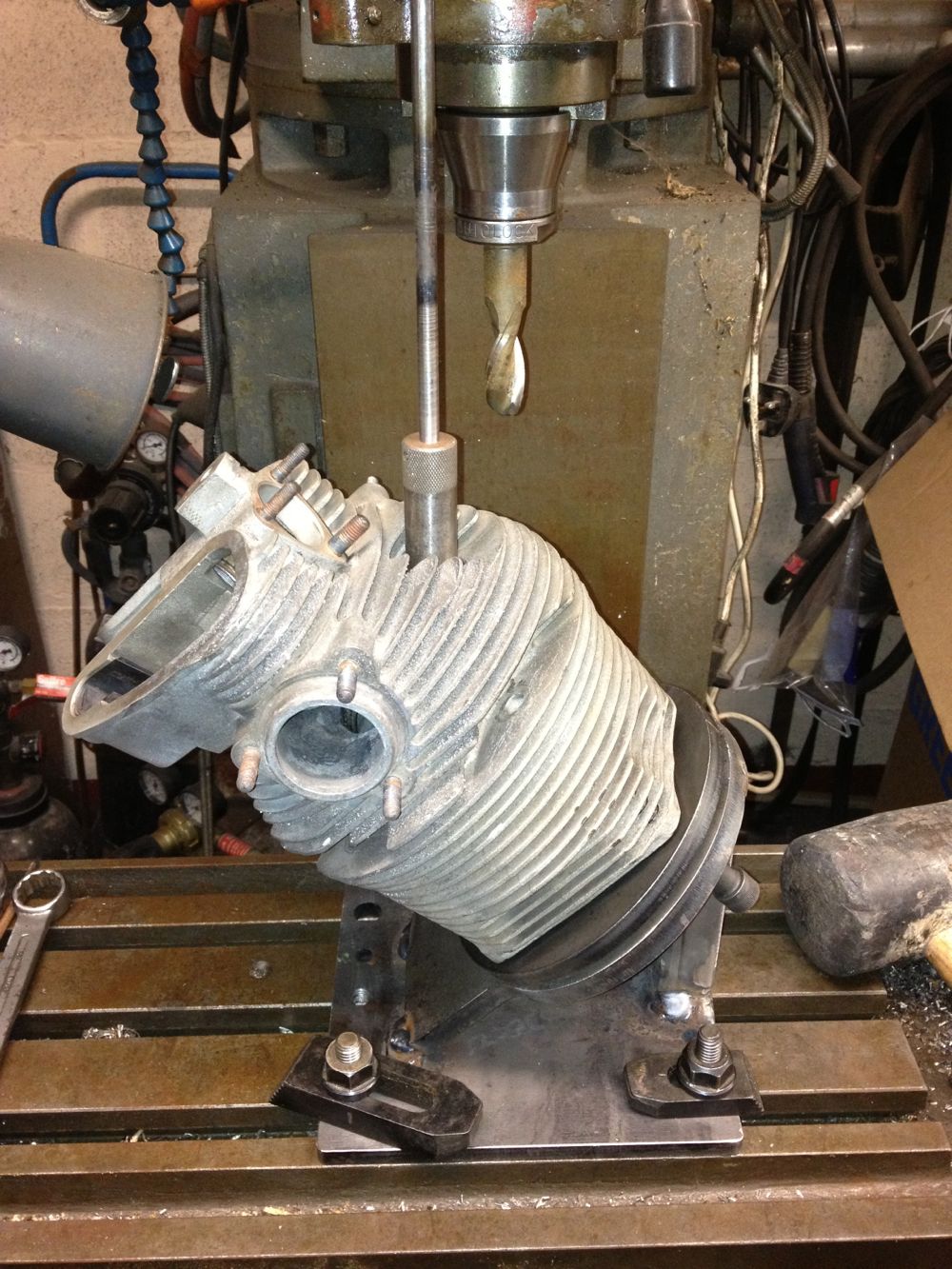
The cylinder is slid onto a turned down liner, and clamped in situ. Then we locate the centre of the original spark plug.
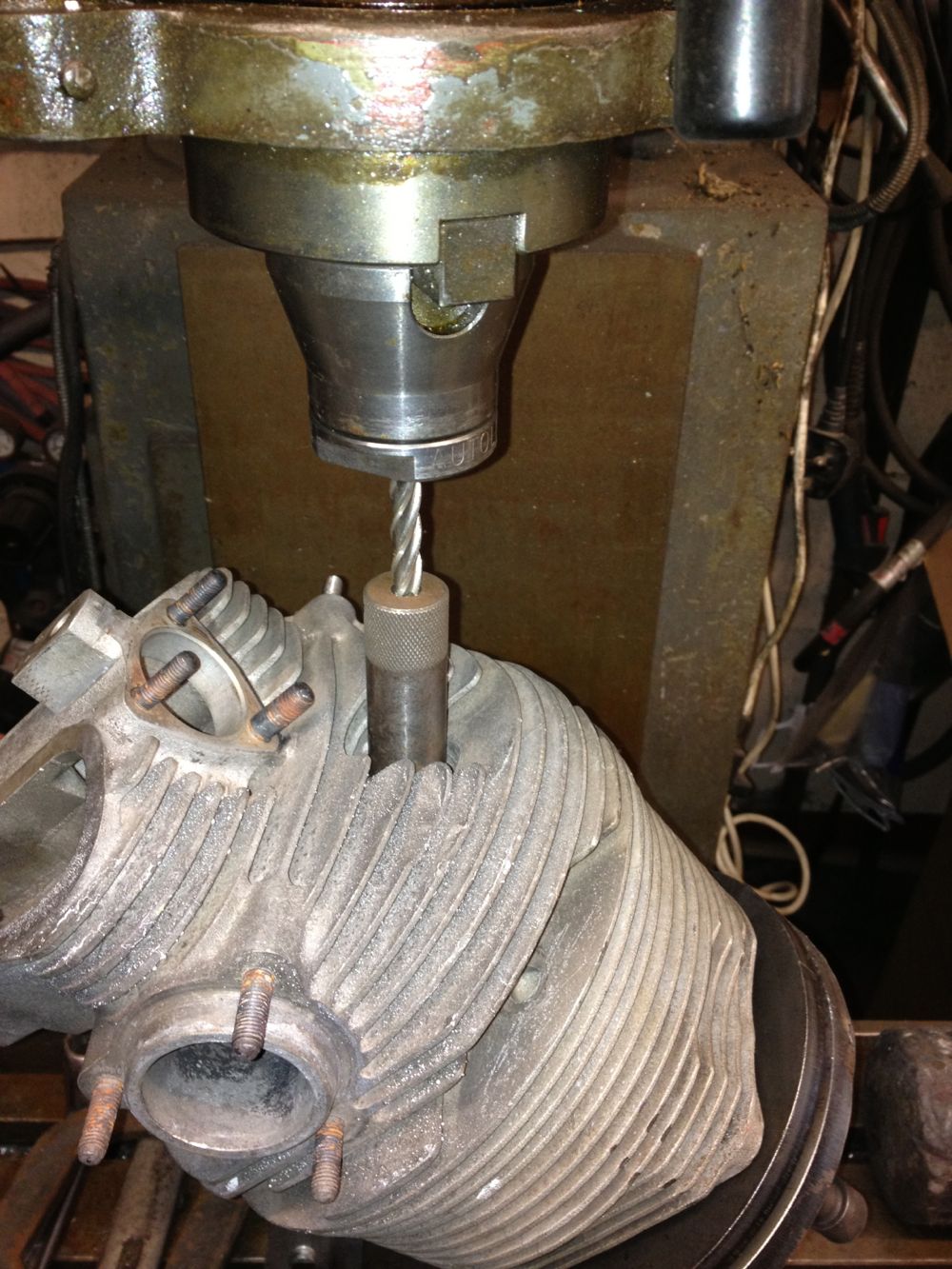
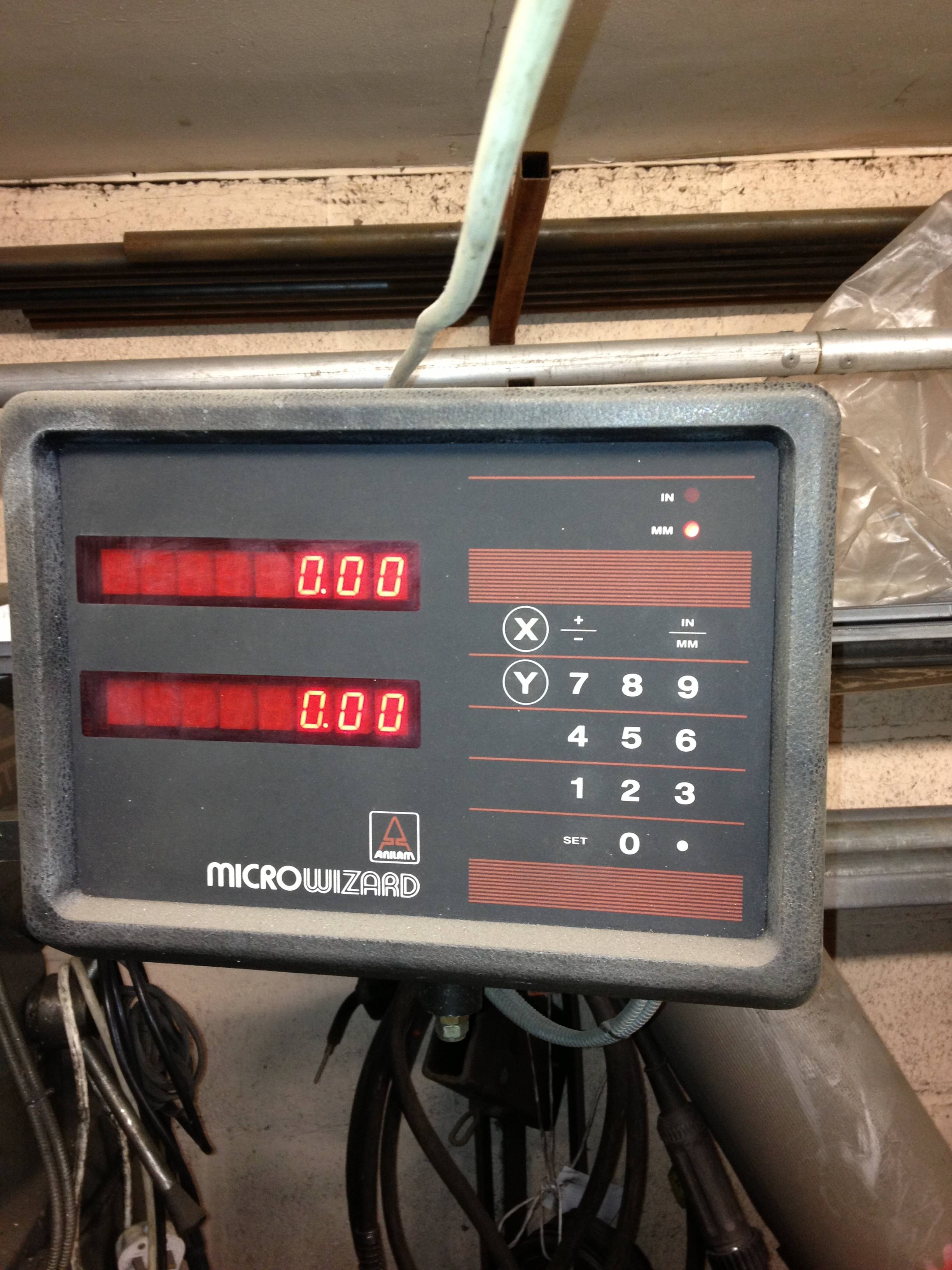
You have to watch you have enough clearance, and in my case I didn’t have enough height to use the larger milling cutters and associated collets. This mill uses Clarkson screwed shank milling tools, so I needed some long series ones for this kind of work. Unfortunately the first operation is to drill the spark plug hole, actually it isn’t, because i used a 20mm diameter slot drill to remove the fins and create a flat surface for a stock 118º HSS twist drill. When I wound the mill table fully down I couldn’t fit the larger INT 40 collet chuck, so I am looking at shortening the jig, angling the head at 45º, or better still, as fellow Panhardista Jean Paul Cesar suggested ”put the milling head horizontal”.
The latter idea is quite appealing, but that’s assuming the mill table can go high enough, and I’ll have to remove the boring bar from the other end of the mill table. I will know for sure tomorrow, and as I don’t have a surface block to place the jig on and hold it down, I might end up cutting the jig down yet, as I thought previously.
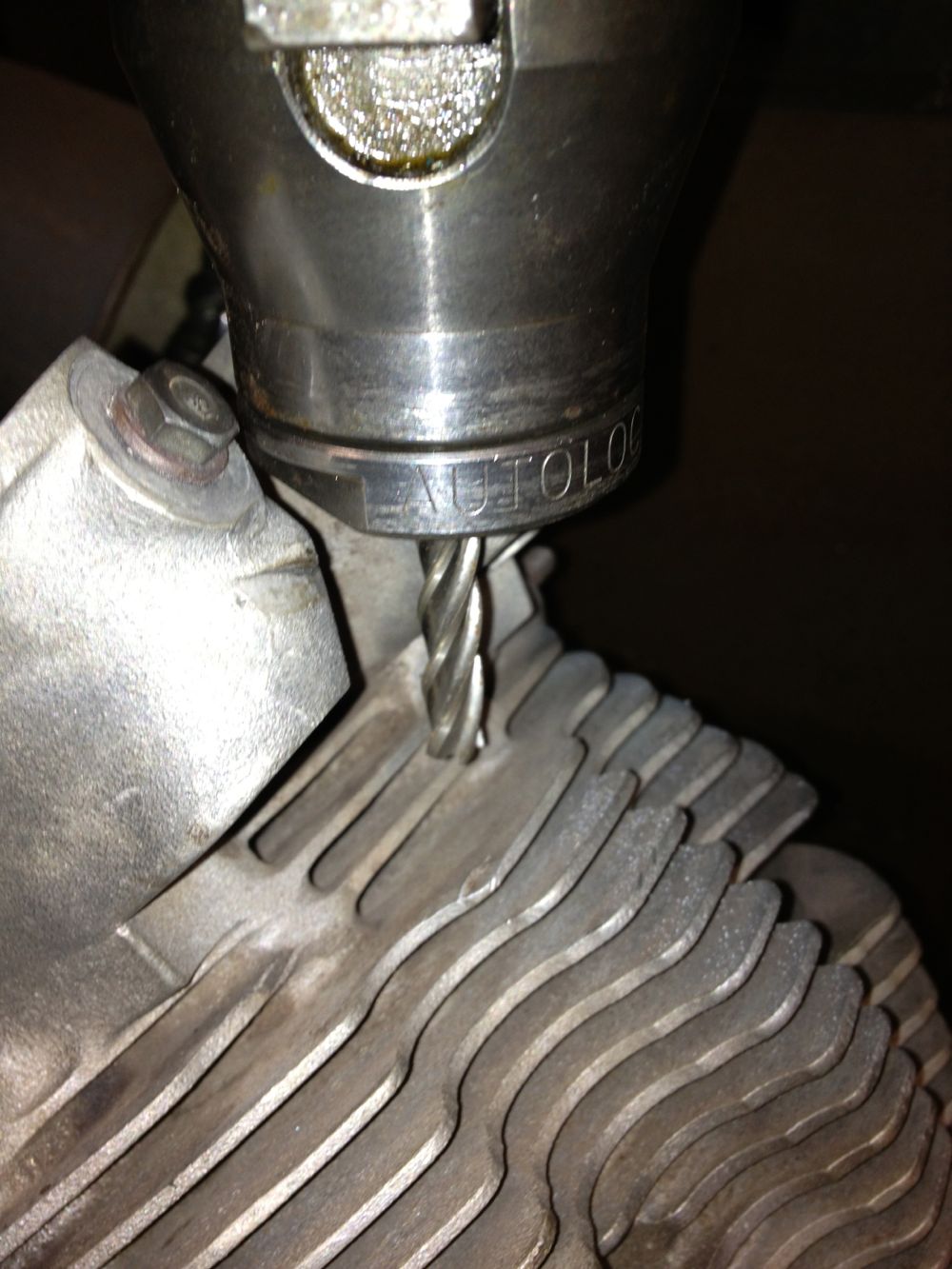
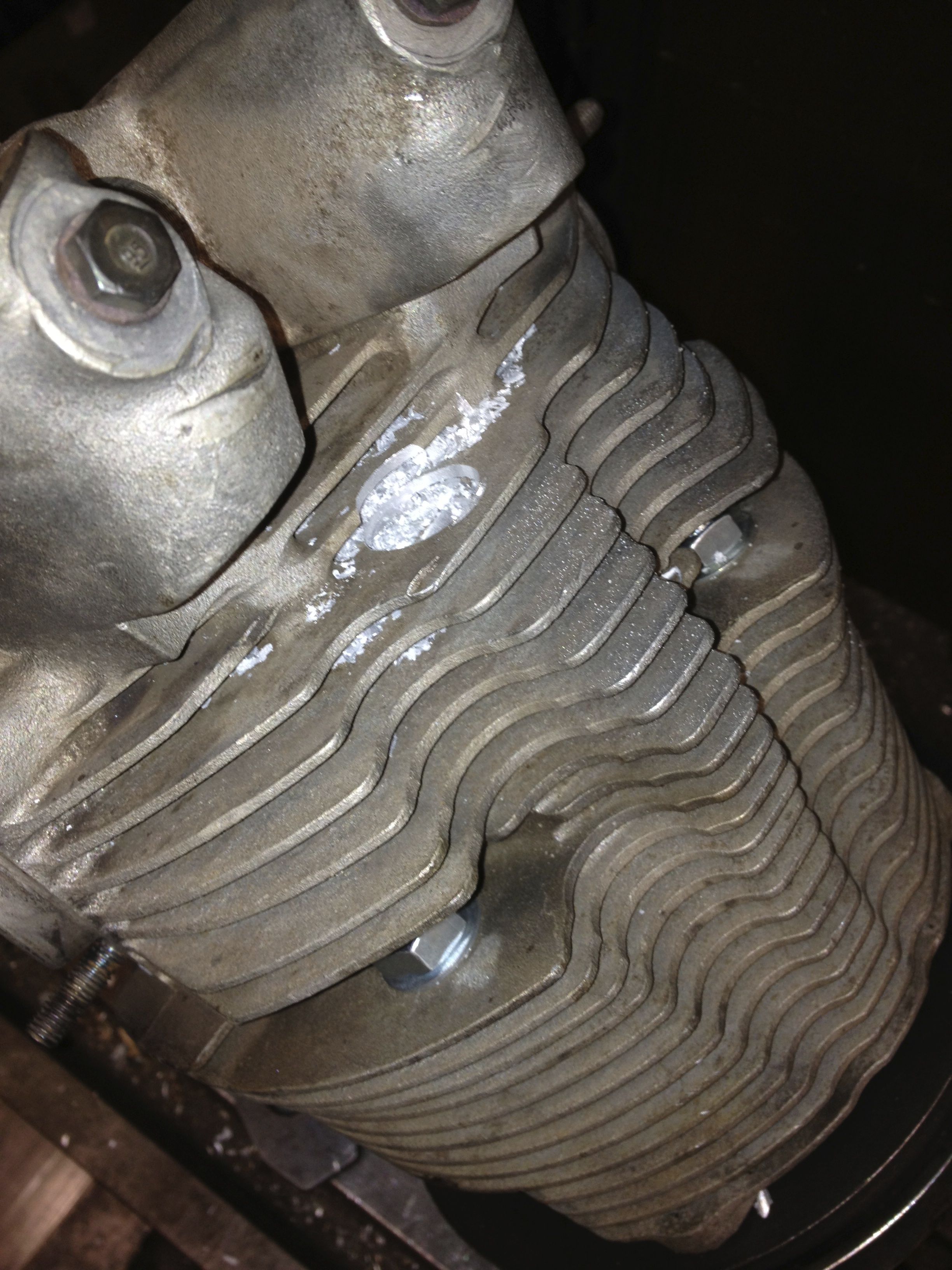
I still managed to do a little bit, here is the cylinder after the 20mm slot drill has cut through the fins, whilst the cylinder awaits the Ø12.5 tapping drill (for the M14 x 1.50 spark plug thread).
If you look at the Panhard combustion chambers you can see the spark plug angle is less than ideal, and there is evidence of electrode shielding too, so Brian’s engine will have surface
discharge spark plugs, which are at a disadvantage at low speed, & lean mixtures, so fitting an extra spark plug will negate some of this.
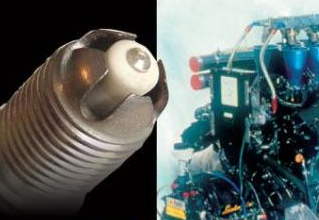
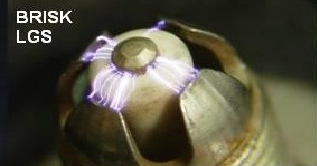
How do you twin plug a cylinder?
You’ll need access to a milling machine ideally, worst case a pillar drill and a Dremel. Sequence of events are,
1. Establish existing spark plug position.
2. rotate cylinder 180º.
3. Drill, tap & mill the spark plug recess.
4. Mill the fins to allow for spanner access.
Here is the start of my jig, which was some reused components from the crankshaft rig, and the honing clamp parts.
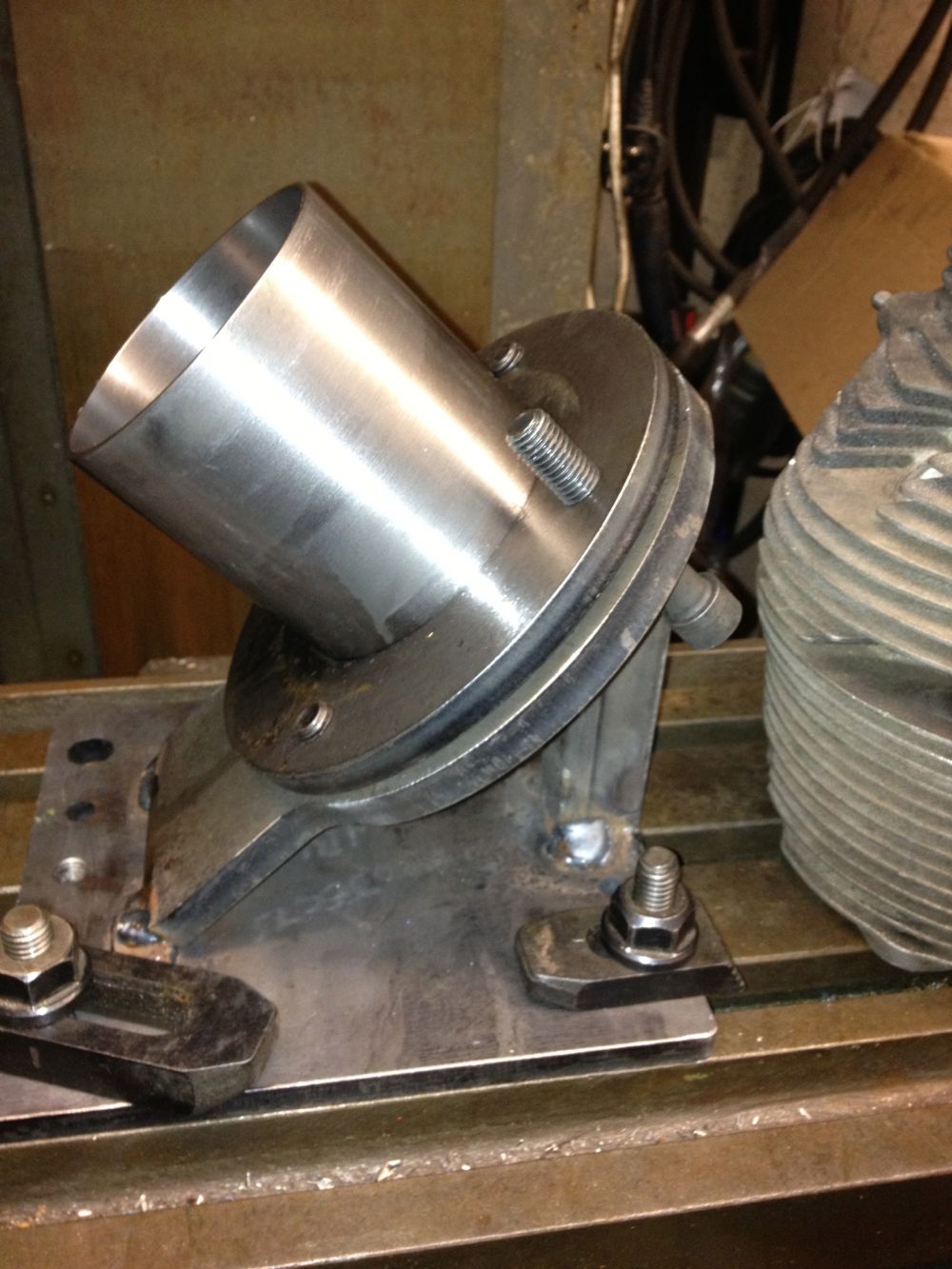
Checking everything is vertical and aligned
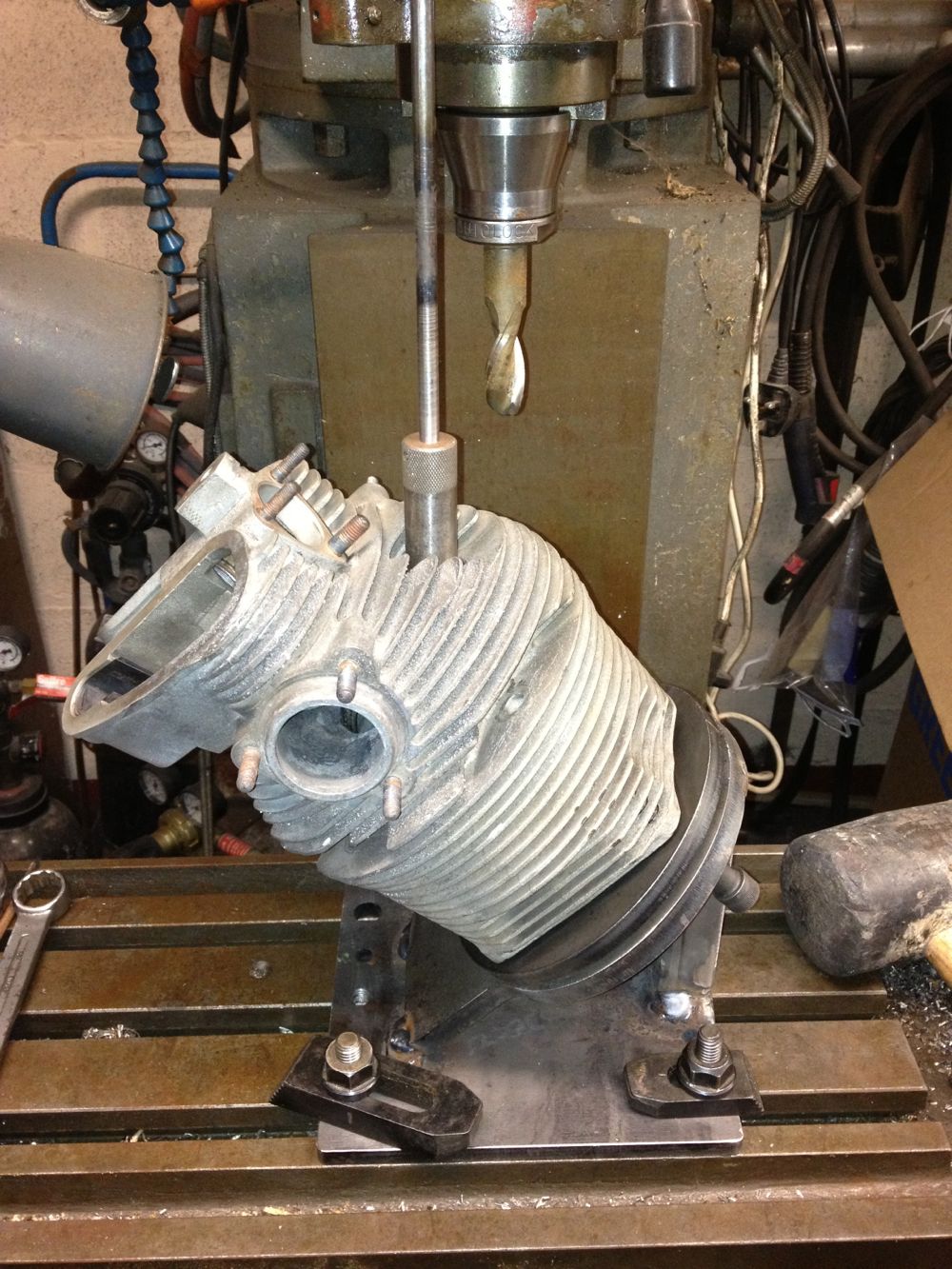
The cylinder is slid onto a turned down liner, and clamped in situ. Then we locate the centre of the original spark plug.
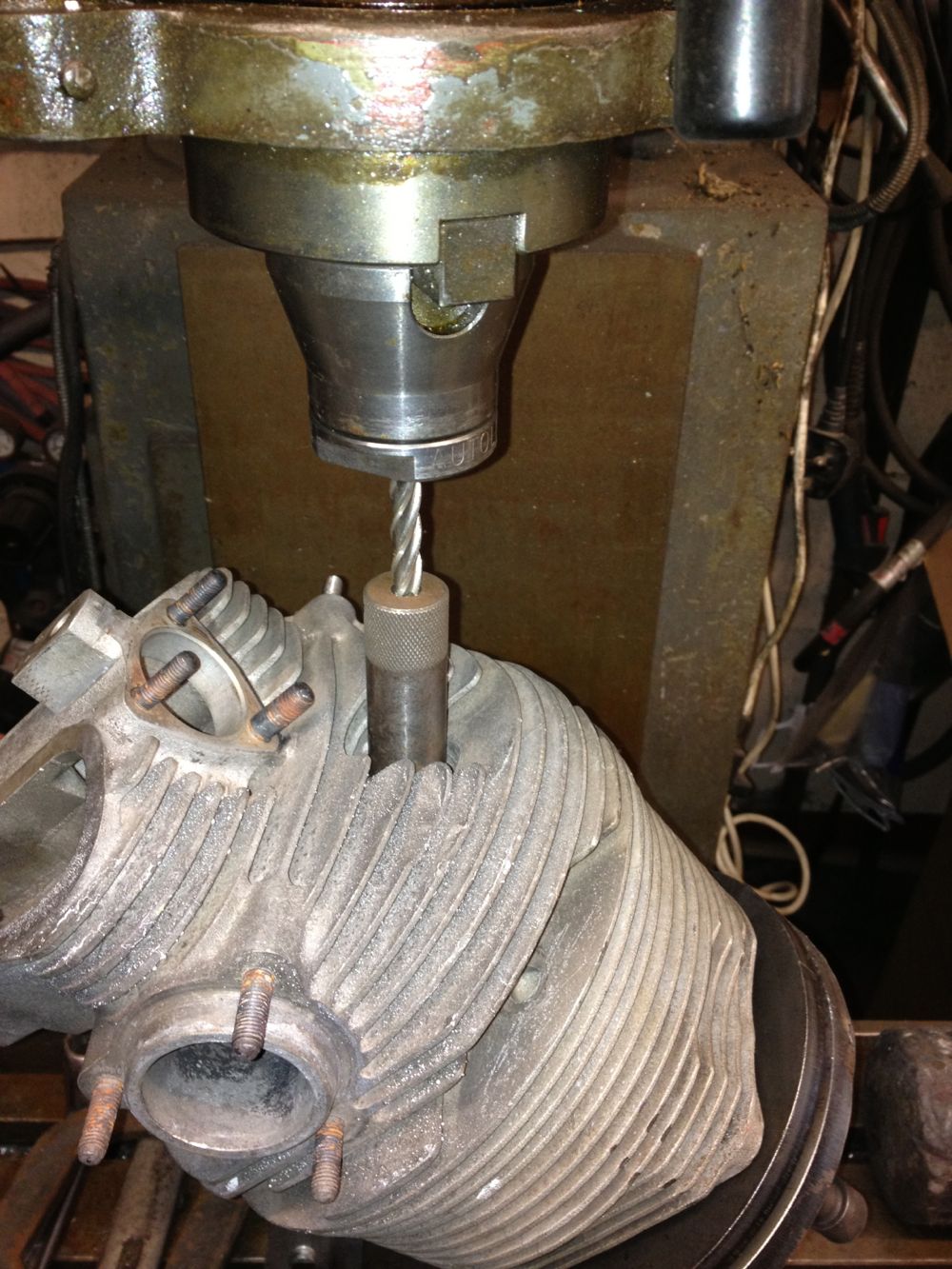
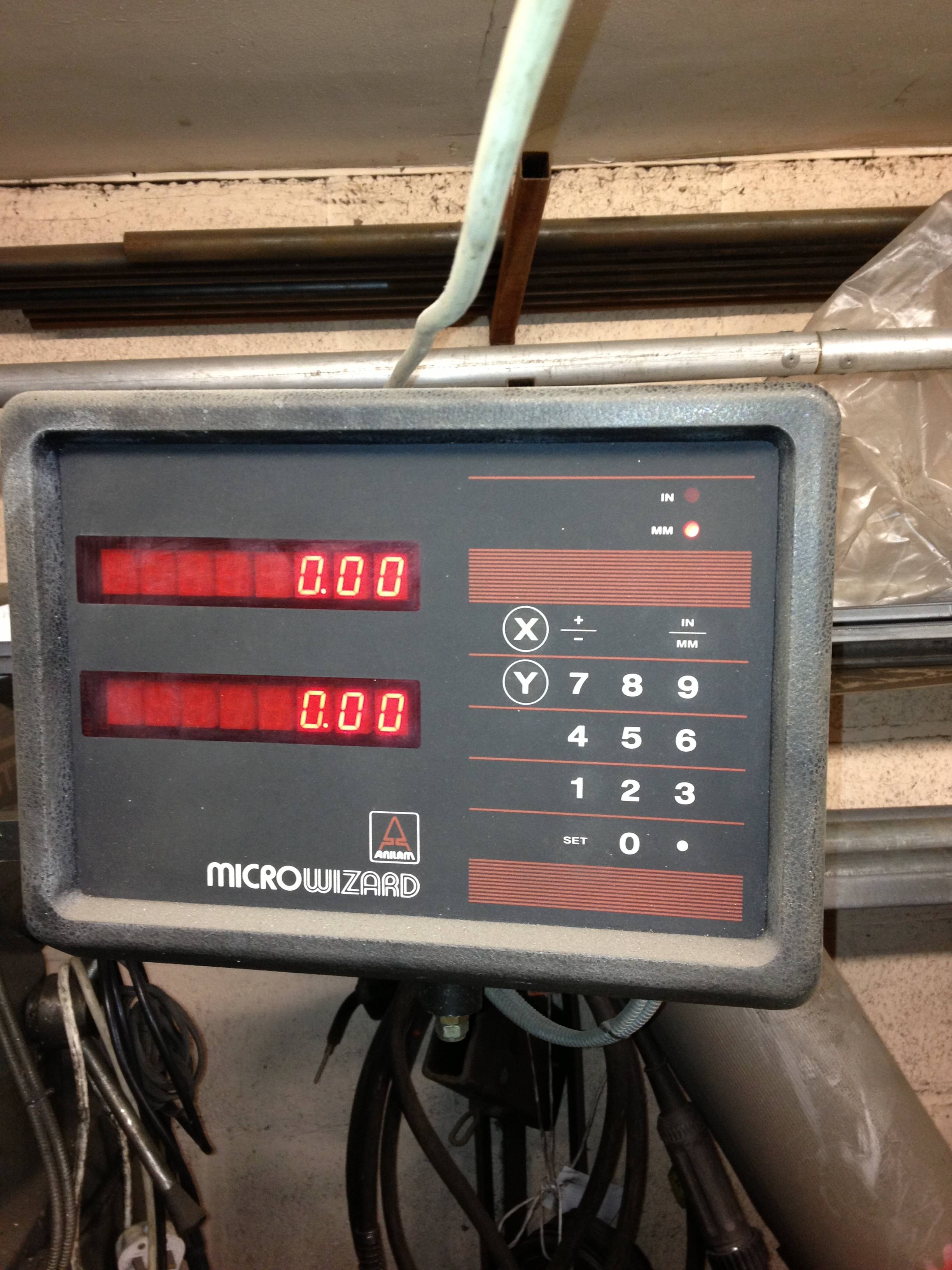
You have to watch you have enough clearance, and in my case I didn’t have enough height to use the larger milling cutters and associated collets. This mill uses Clarkson screwed shank milling tools, so I needed some long series ones for this kind of work. Unfortunately the first operation is to drill the spark plug hole, actually it isn’t, because i used a 20mm diameter slot drill to remove the fins and create a flat surface for a stock 118º HSS twist drill. When I wound the mill table fully down I couldn’t fit the larger INT 40 collet chuck, so I am looking at shortening the jig, angling the head at 45º, or better still, as fellow Panhardista Jean Paul Cesar suggested ”put the milling head horizontal”.
The latter idea is quite appealing, but that’s assuming the mill table can go high enough, and I’ll have to remove the boring bar from the other end of the mill table. I will know for sure tomorrow, and as I don’t have a surface block to place the jig on and hold it down, I might end up cutting the jig down yet, as I thought previously.
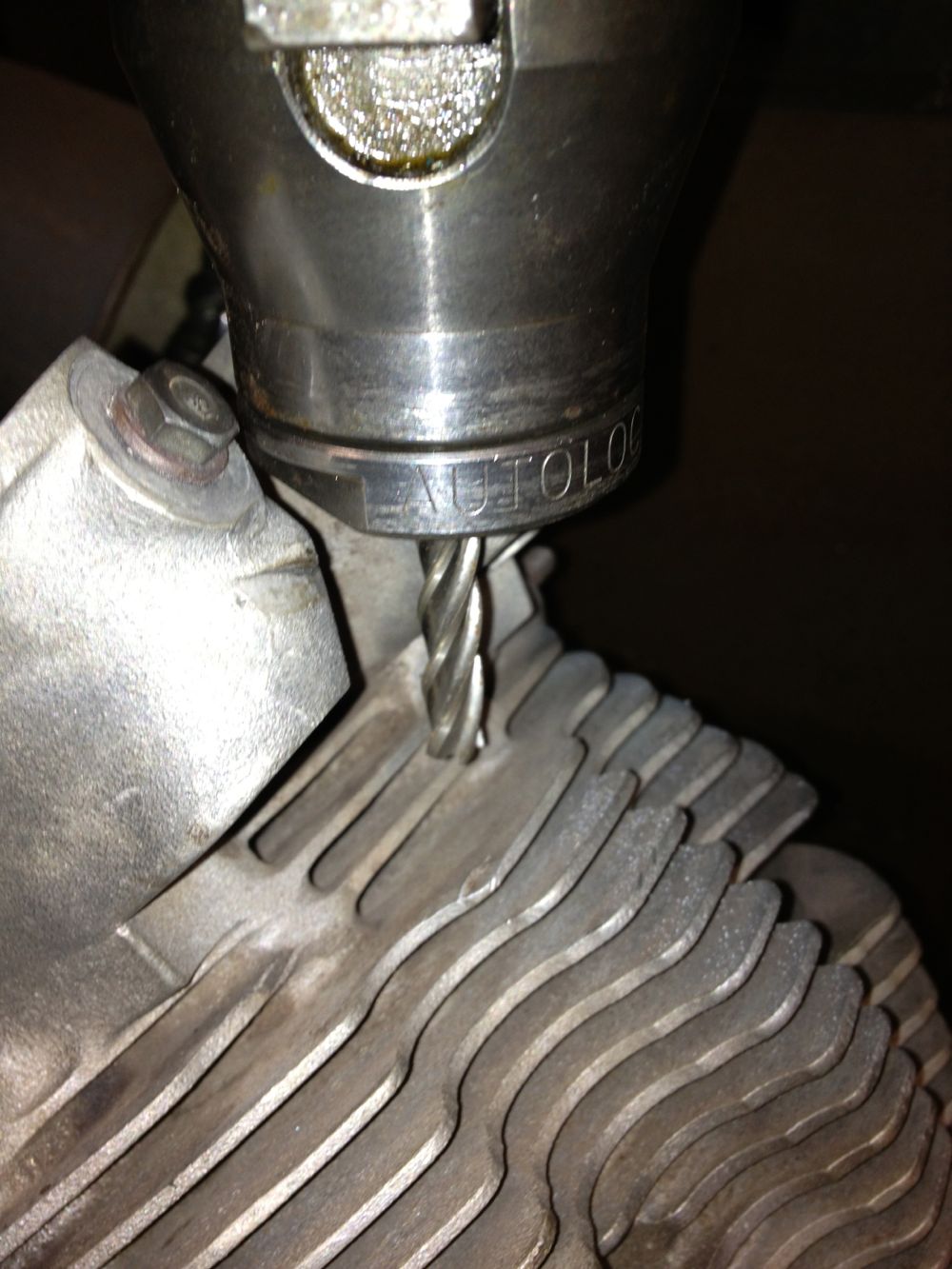
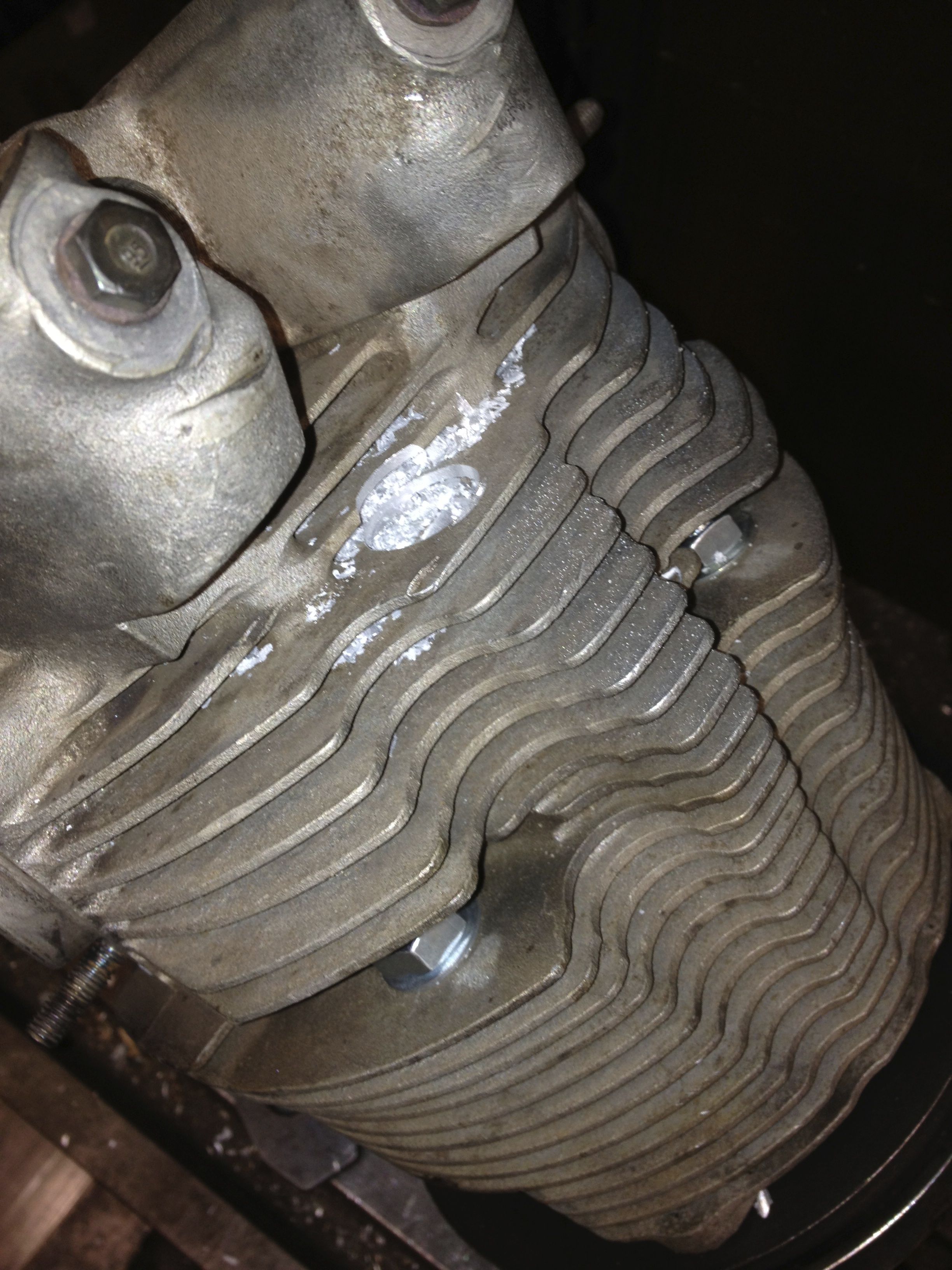
I still managed to do a little bit, here is the cylinder after the 20mm slot drill has cut through the fins, whilst the cylinder awaits the Ø12.5 tapping drill (for the M14 x 1.50 spark plug thread).
blog comments powered by Disqus