Jul 2011
Panhard cylinder
Saturday 09 July 2011 Filed in: Panhard Cylinder
Panhard cylinder heads and barrels are a one piece assembly, very similar to early aero engines, which incidentally removes any chance of head gasket failures, but this makes machining them awkward. Technology has moved on and it’s not the norm to manufacture engines like this, and in fact Porsche engines pro rata manage to make more horsepower using similar materials incorporating head gaskets, without suffering from reliability issues.
For my engine work, it was always going to be necessary to revisit the cylinder construction, and again many years ago I separated a head from a cylinder, as a design exercise to investigate the feasibility of modifying these components, and making new parts. I remember doing this in the lathe, and the cooling fins from the barrel only just cleared the toolholder, but when they were separated and you could see the individual pieces, it was obvious to me this was the only way to go, if you wanted to bring the engines into the 21st century. Panhard tapered the liners, and used split skirt pistons with hemispherical combustion chambers, which was OK in the 1940s, but current combustion chamber thinking is moving towards minimal surface areas and squish, with reduced ignition advance.
Cylinder and coating technology has moved on as well, so whereas VW would use a Biral cylinder in the 80’s, quite similar to a Panhard with a steel liner and aluminium finning, others in motorcycling and karting were using all aluminium construction for their cylinder construction with Nikasil plating for the piston surfaces. Early plating processes were responsible for a few engine failures over time, with plating separation at the head gasket/ cylinder interfaces causing all sorts of issues, especially in higher performance engines with detonation.
Fortunately, thanks in part to the space programme and the accelerated development of ceramics, there are better alternatives available now with amazing potential. Aluminium is now used in tool steel injection moulding machines with coatings applied, that offer better thermal and longer life than their steel equivalents, plus the coating deposition processes have become much better environmentally and from a tribological viewpoint are now second to none and so used extensively in high performance engines.
What does this mean for Panhards, well you could remove the heads, make new cylinders with increased finning to dissipate the heat, just like others did in WWII, as air cooled engine performance was boosted in fighter aircraft. At the same time, eliminate the steel liner using modern coating technology, and safely increase the performance margins, as a cooler cylinder would keep heat away from the cylinder heads, and no liner would negate differing thermal expansion rates. The coatings technology would secure long life, corrosion protection and a restoration route if required.
A standard cylinder has eight fins under the head like the drawing below.
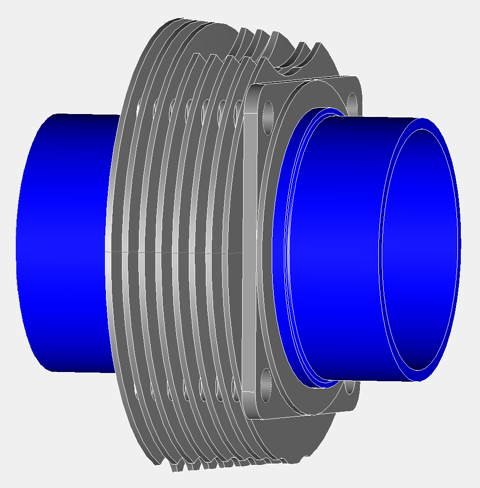
Mine will have...well you have to wait! Anyway there are other priorities first, because there’s no use making cylinders that increase performance, as the crankshaft is undoubtedly the weakest link. Peter Breed in Holland offers a first class crankshaft service, with bespoke connecting rods and new pistons to rebored OEM cylinders. It is a good system, and was the most cost effective route at the time, and probably still is. How do I know, well I worked with Peter on this solution, but it relies on a having a salvageable crankshaft at the start and that’s why I am developing a new remanufacturing process, because I want to salvage these tired, pitted and corroded crankshafts.
For my engine work, it was always going to be necessary to revisit the cylinder construction, and again many years ago I separated a head from a cylinder, as a design exercise to investigate the feasibility of modifying these components, and making new parts. I remember doing this in the lathe, and the cooling fins from the barrel only just cleared the toolholder, but when they were separated and you could see the individual pieces, it was obvious to me this was the only way to go, if you wanted to bring the engines into the 21st century. Panhard tapered the liners, and used split skirt pistons with hemispherical combustion chambers, which was OK in the 1940s, but current combustion chamber thinking is moving towards minimal surface areas and squish, with reduced ignition advance.
Cylinder and coating technology has moved on as well, so whereas VW would use a Biral cylinder in the 80’s, quite similar to a Panhard with a steel liner and aluminium finning, others in motorcycling and karting were using all aluminium construction for their cylinder construction with Nikasil plating for the piston surfaces. Early plating processes were responsible for a few engine failures over time, with plating separation at the head gasket/ cylinder interfaces causing all sorts of issues, especially in higher performance engines with detonation.
Fortunately, thanks in part to the space programme and the accelerated development of ceramics, there are better alternatives available now with amazing potential. Aluminium is now used in tool steel injection moulding machines with coatings applied, that offer better thermal and longer life than their steel equivalents, plus the coating deposition processes have become much better environmentally and from a tribological viewpoint are now second to none and so used extensively in high performance engines.
What does this mean for Panhards, well you could remove the heads, make new cylinders with increased finning to dissipate the heat, just like others did in WWII, as air cooled engine performance was boosted in fighter aircraft. At the same time, eliminate the steel liner using modern coating technology, and safely increase the performance margins, as a cooler cylinder would keep heat away from the cylinder heads, and no liner would negate differing thermal expansion rates. The coatings technology would secure long life, corrosion protection and a restoration route if required.
A standard cylinder has eight fins under the head like the drawing below.
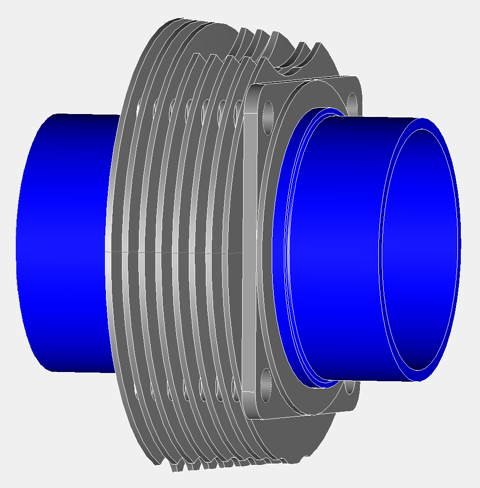
Mine will have...well you have to wait! Anyway there are other priorities first, because there’s no use making cylinders that increase performance, as the crankshaft is undoubtedly the weakest link. Peter Breed in Holland offers a first class crankshaft service, with bespoke connecting rods and new pistons to rebored OEM cylinders. It is a good system, and was the most cost effective route at the time, and probably still is. How do I know, well I worked with Peter on this solution, but it relies on a having a salvageable crankshaft at the start and that’s why I am developing a new remanufacturing process, because I want to salvage these tired, pitted and corroded crankshafts.
Comments
Panhard crankshaft pulley
Sunday 03 July 2011 Filed in: Panhard Ignition
I recently bought a newer CAD package, so rather than use Ashlar Vellum from the late 80’s on a G4 Cube, I can now use my Intel iMac & MacBook Pro, which are significantly faster. The software also has a number of export options, and I recently did a test .dxf file export to a laser cutting company, and everything translated between the differing computer platforms & softwares flawlessly. The parts were used in the engine stand.
To get used to the software some more, I started to redraw some Panhard components, that I had drawn up years ago, but were in the older format. This is the start of the new dynamo pulley, which is really going to become an alternator pulley. It should be obvious which is which if you’ve seen the components before, but original part is the bottom image, with the my updated version on top.
Final timing gear design, 60-2 drawn, or pulley drive belt section not fixed yet, as aftermarket low cost alternator or the VR sensor location isn’t finalised.
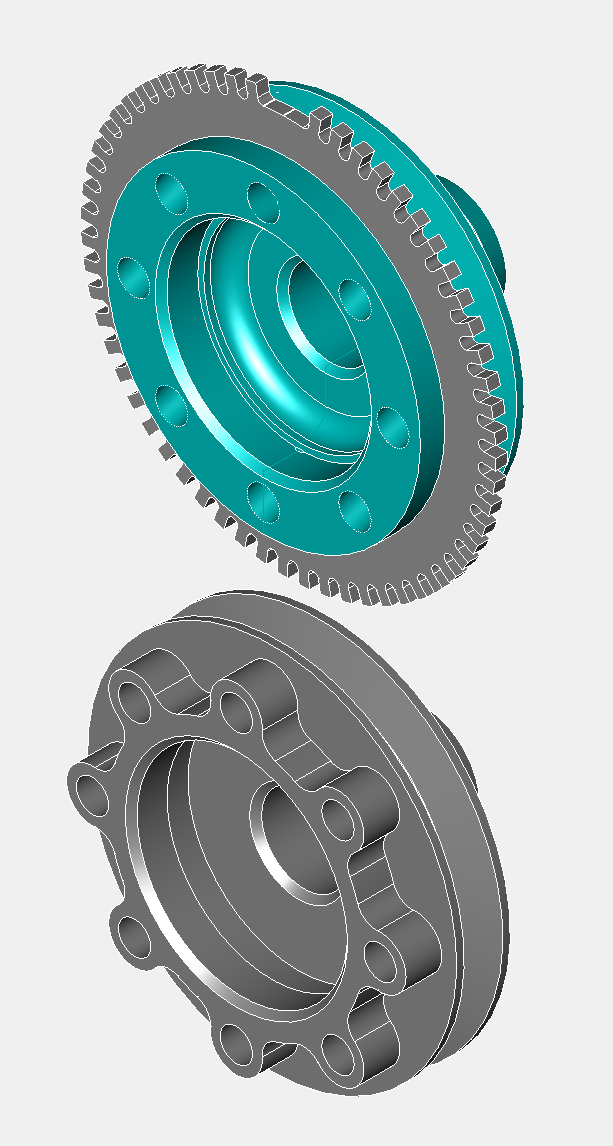
To get used to the software some more, I started to redraw some Panhard components, that I had drawn up years ago, but were in the older format. This is the start of the new dynamo pulley, which is really going to become an alternator pulley. It should be obvious which is which if you’ve seen the components before, but original part is the bottom image, with the my updated version on top.
Final timing gear design, 60-2 drawn, or pulley drive belt section not fixed yet, as aftermarket low cost alternator or the VR sensor location isn’t finalised.
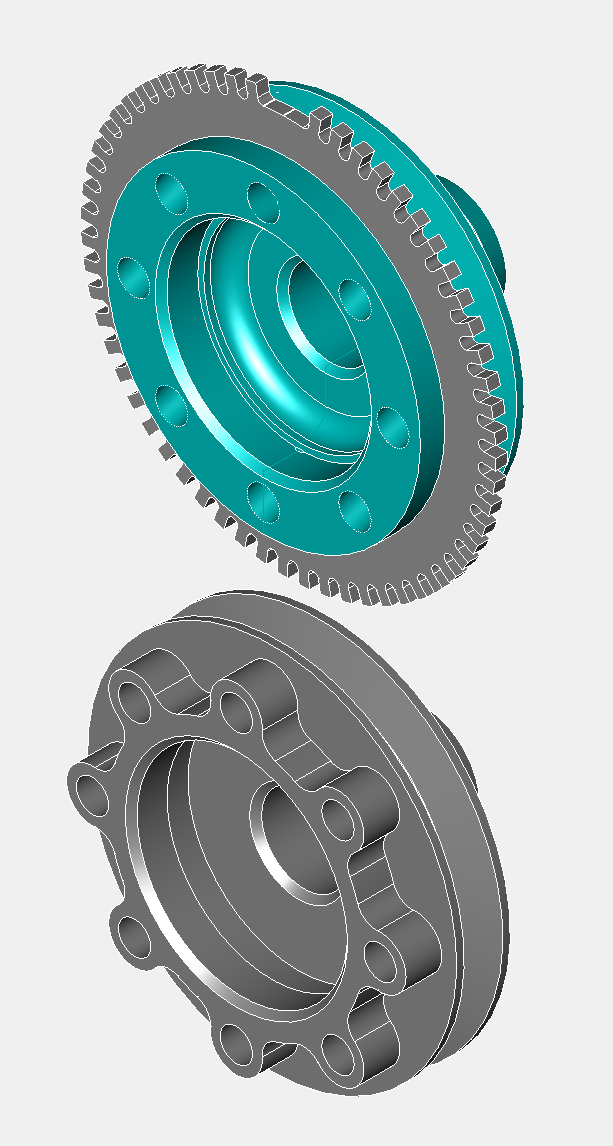