Oct 2011
Panhard trigger wheel testing
Sunday 02 October 2011 Filed in: Panhard Ignition
Another few hours spent on this, testing various iterations of the firmwares with my cased MicroSquirts, and revisiting yesterdays efforts, as I made a number of teeth input error part way through my previous attempts. This only affects the early B&G firmware and MSExtra as they need the correct value inputting, whereas the later B&G 3.760 has an auto detect function called Auto Trigger.
A quick screenshot of TunerStudio doing its stuff using the logging tools. The cyan columns are the 11 teeth, the gap the 12th missing tooth, and the red line on the bottom is the Sync errors, and because this line is straight there are none. Using MSExtra 3.1.0, I can get reliable sync from 45 rpm up to 11800 rpm using the Renault sensor and a 2mm air gap. I think if the trigger wheel is made thicker, it will allow me to increase the air gap to nearer 3mm, and I might make the teeth slightly less wide too.
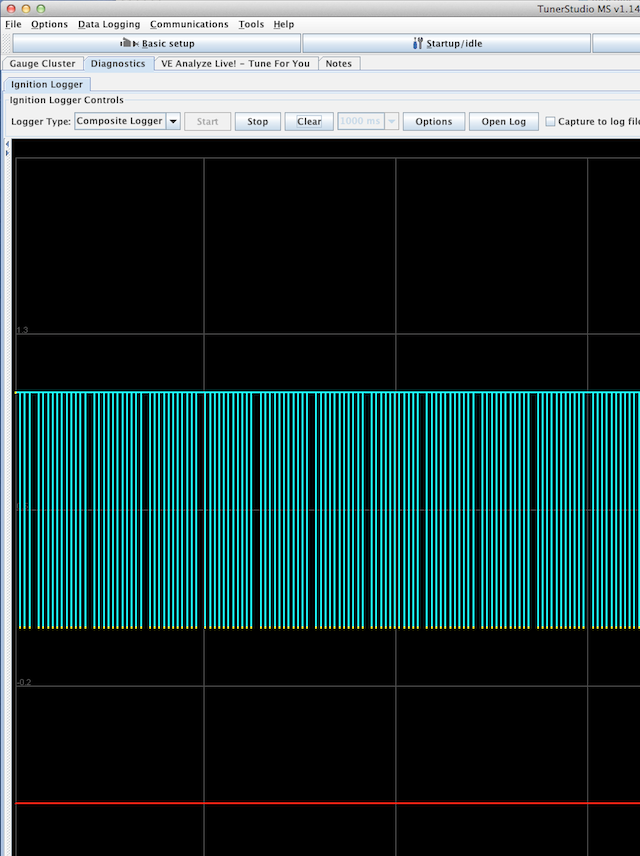
The screenshot below shows the tooth pattern, the 11vertical lines roughly the same size are the physical bumps or teeth, and the tallest column is the missing tooth area. This is what the ECU is seeing, but as this is using the motorised engine rig, so the variances between the 11 teeth are not very pronounced. However when this is used on a real engine the compression effects and the resulting slowing down of the trigger wheel attached to the crankshaft, shows itself in bigger variances in height.
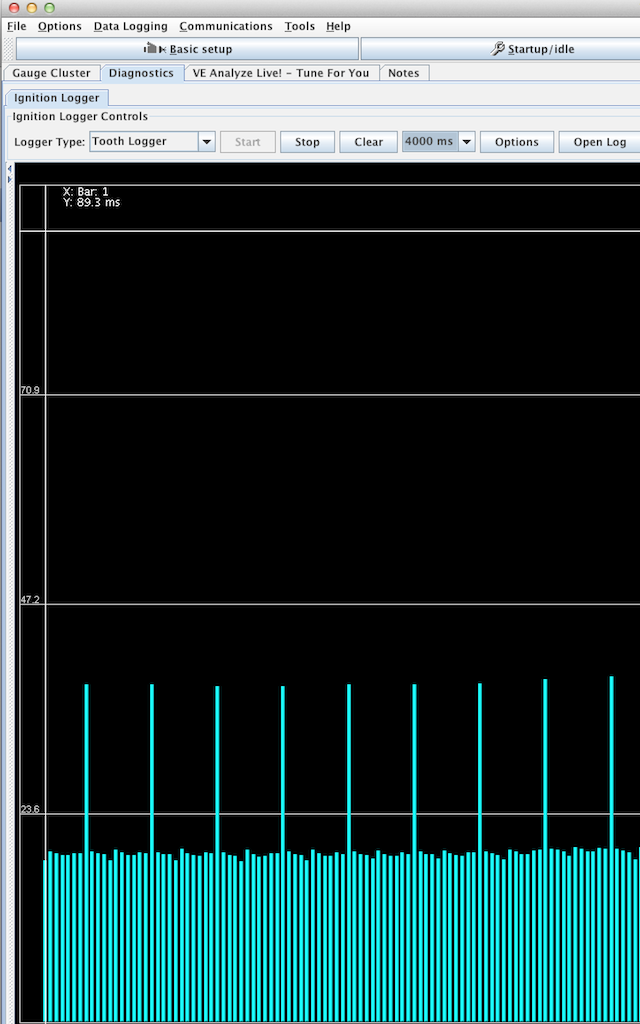
A quick screenshot of TunerStudio doing its stuff using the logging tools. The cyan columns are the 11 teeth, the gap the 12th missing tooth, and the red line on the bottom is the Sync errors, and because this line is straight there are none. Using MSExtra 3.1.0, I can get reliable sync from 45 rpm up to 11800 rpm using the Renault sensor and a 2mm air gap. I think if the trigger wheel is made thicker, it will allow me to increase the air gap to nearer 3mm, and I might make the teeth slightly less wide too.
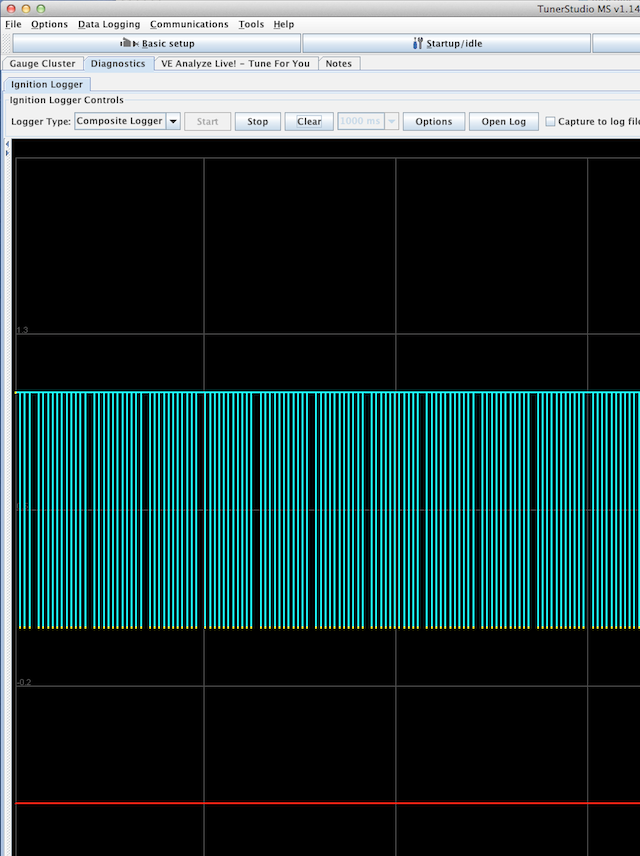
The screenshot below shows the tooth pattern, the 11vertical lines roughly the same size are the physical bumps or teeth, and the tallest column is the missing tooth area. This is what the ECU is seeing, but as this is using the motorised engine rig, so the variances between the 11 teeth are not very pronounced. However when this is used on a real engine the compression effects and the resulting slowing down of the trigger wheel attached to the crankshaft, shows itself in bigger variances in height.
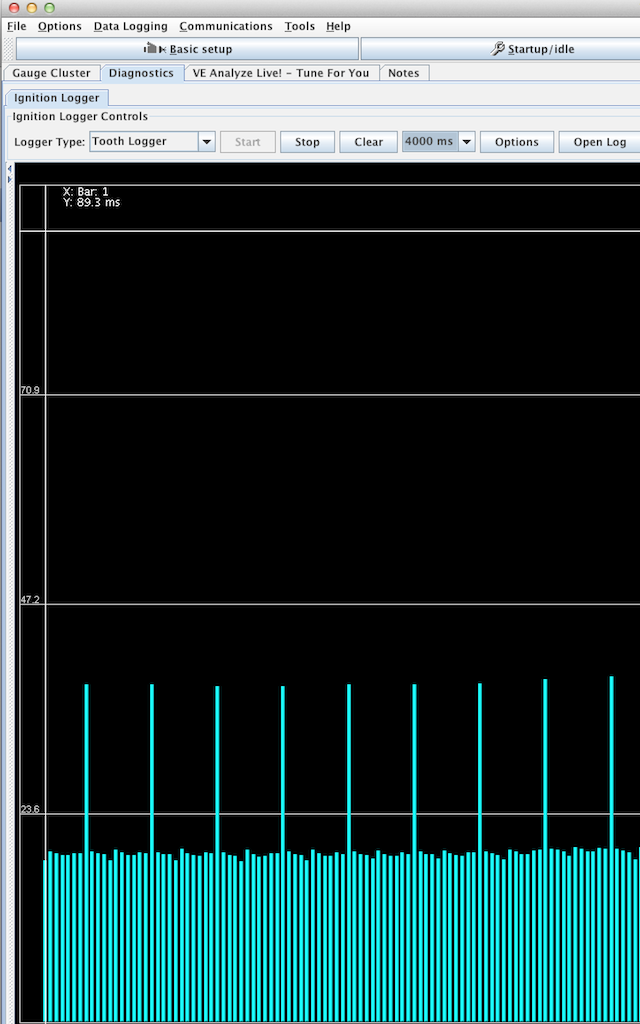
Comments
Panhard crankshaft pulley on EFI rig
Saturday 01 October 2011 Filed in: Panhard Ignition
I managed to get a few timing wheels laser cut the other day, and the idea was to combine these with a Renault crankshaft sensor, so that I can create a timing trigger for the electronic ignition. I had done this with an earlier project, but now wanted to refine the set up further to allow for the fuel injection mods that will follow from this.
Here’s a pic of the first design effort, and there’s me thinking that a 3mm thick wheel would be sufficient for a 2mm sensor tip. At first it didn’t seem like it would be, and the disturbing thing is there is a slight eccentricity with these OEM pulleys, so a wider wheel might be useful to combat this. The reason why it wasn’t working as well as it should have done, was because I was putting the wrong values into the Number of Teeth box. I was inputting 8-1, when it was plainly a 12-1 wheel!

I was also swapping various v2 MicroSquirts & a v3 beta running different EFI firmwares including MSExtra 3.1 and, B&G 2.890, 3.430 & 3.760.
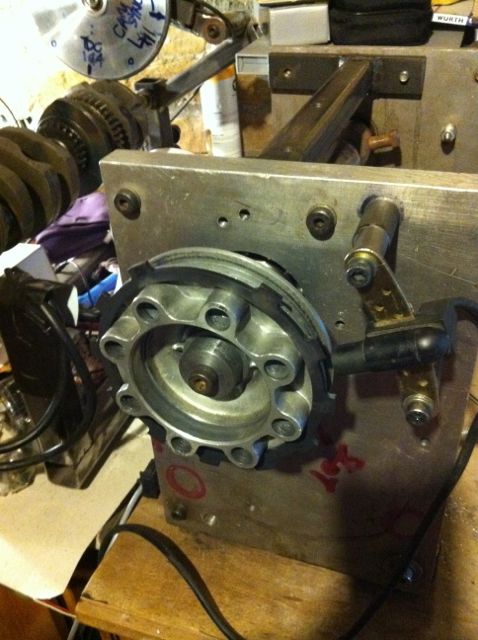
This 12-1 wheel design worked OK up to 3000 rpm, but then dropped out of sync, whereas the 6mm thick 36-1 wheel using the same sensor worked faultlessly from 50-11780 rpm, so despite the initial input error, the trigger wheel is too thin.
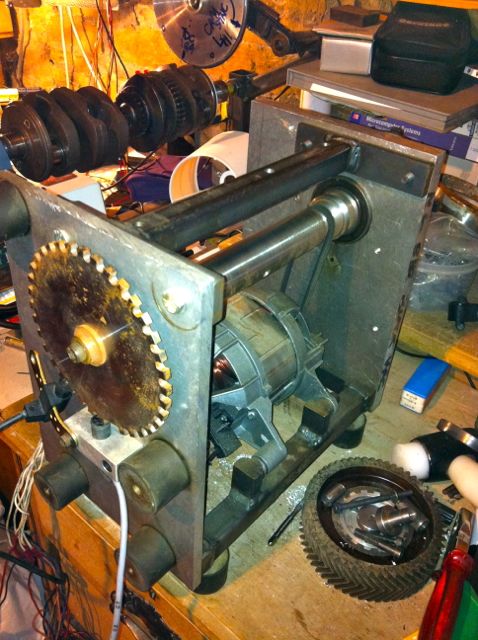
This is the old washing machine motor from a 1986 Hotpoint ℅ Siemens Gmbh dropped into my DIY engine rig. I have had to fit a poly-vee belt reduction gear, as this thing will rev to 22,000 RPM in 1:1 mode!
Note. Bottom right, inside the chevron cut fibre camshaft timing gear are the revised oil light pistons I made in the 1990’s to combat the lubrication faults with the Panhard engine. The picture below shows an incomplete one, with the revised lubrication to the timing gear (there is a relief valve, ball, spring with a set screw yet to be inserted in the middle).
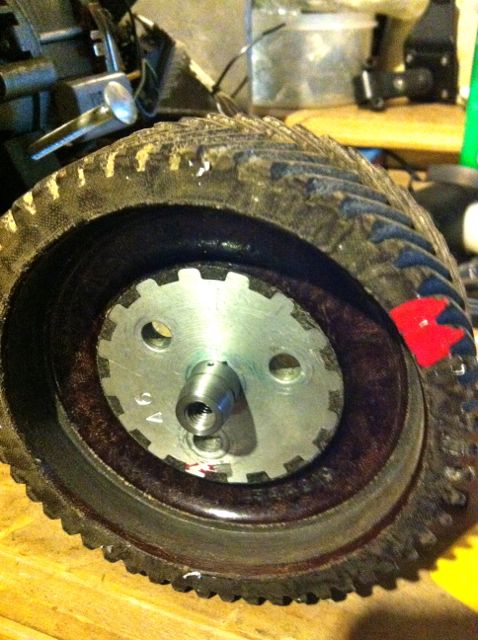
Also can you spot the crankshaft & cam rig in the background, above this picture, which is still being used to develop the MicroSquirt based EFI systems for the GTS1000 & Thunderace motorcycle engines
Here’s a pic of the first design effort, and there’s me thinking that a 3mm thick wheel would be sufficient for a 2mm sensor tip. At first it didn’t seem like it would be, and the disturbing thing is there is a slight eccentricity with these OEM pulleys, so a wider wheel might be useful to combat this. The reason why it wasn’t working as well as it should have done, was because I was putting the wrong values into the Number of Teeth box. I was inputting 8-1, when it was plainly a 12-1 wheel!

I was also swapping various v2 MicroSquirts & a v3 beta running different EFI firmwares including MSExtra 3.1 and, B&G 2.890, 3.430 & 3.760.
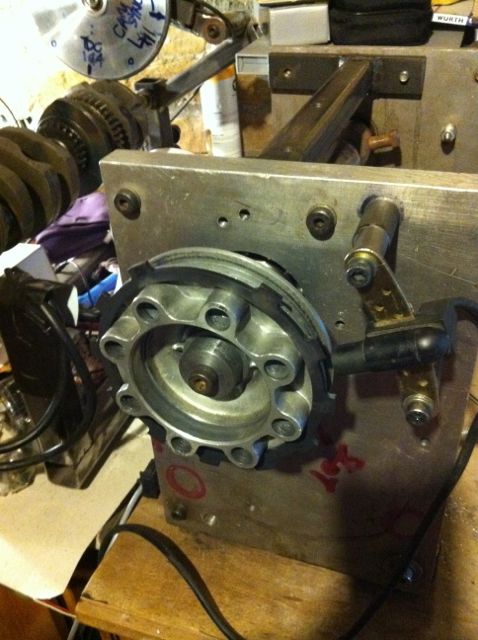
This 12-1 wheel design worked OK up to 3000 rpm, but then dropped out of sync, whereas the 6mm thick 36-1 wheel using the same sensor worked faultlessly from 50-11780 rpm, so despite the initial input error, the trigger wheel is too thin.
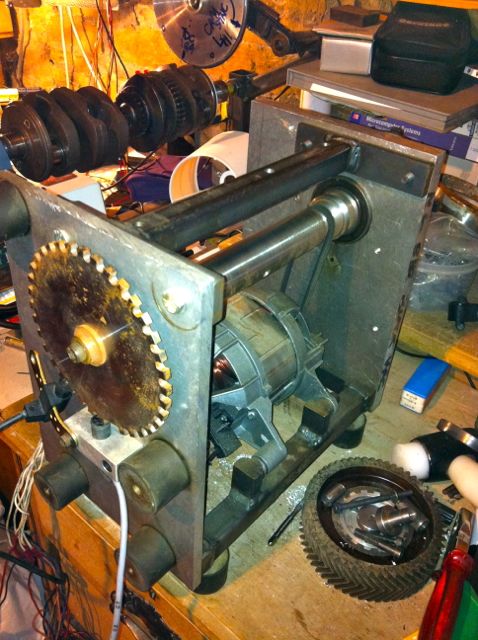
This is the old washing machine motor from a 1986 Hotpoint ℅ Siemens Gmbh dropped into my DIY engine rig. I have had to fit a poly-vee belt reduction gear, as this thing will rev to 22,000 RPM in 1:1 mode!
Note. Bottom right, inside the chevron cut fibre camshaft timing gear are the revised oil light pistons I made in the 1990’s to combat the lubrication faults with the Panhard engine. The picture below shows an incomplete one, with the revised lubrication to the timing gear (there is a relief valve, ball, spring with a set screw yet to be inserted in the middle).
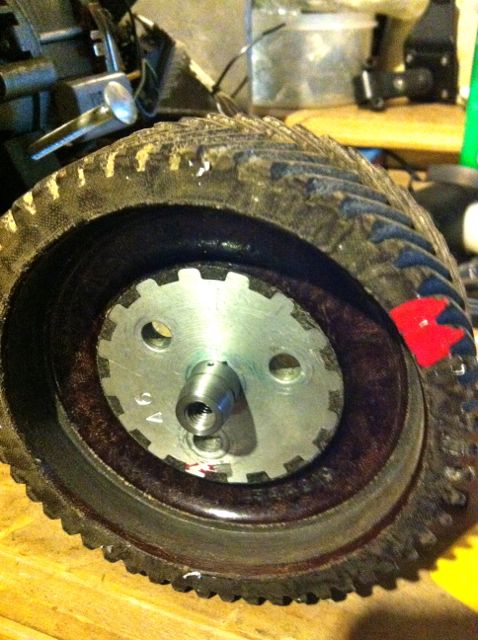
Also can you spot the crankshaft & cam rig in the background, above this picture, which is still being used to develop the MicroSquirt based EFI systems for the GTS1000 & Thunderace motorcycle engines
