Panhard oil filter, article from Panoramique
Sunday 12 April 1998 Filed in: Panhard Oil
I was a club member from many years ago who after disturbing the 17BT’s carcass in a shed clear out, was motivated into rejoining. Along with the vast quantities of junk I unearthed, I found an old engine project sealed in some ice cream tubs. It was the remains of a cartridge oil filter adaptor I had worked on thirteen years ago. I looked at the drawings I had filed away inside the tubs and worked out what I had been thinking about. I asked around to see what other folk were up to re oil & filtration. OK, so a few had bolted on oil coolers via the valve gear oilways at the side of the crankcase, or the upper cylinder banjos, but it seems nobody seized the problem at source, as per more usual lubrication practises.
Why bother you might ask? In the last fifteen years I have been tinkering with air filtration, valve gear modifications, all things Fiat 124 Spider, Fiat twin cam and four stroke motorcycle engines. Researching and rebuilding when required and with respect to lubrication, engines with roller bearing crankshafts & big ends have real oil filtration not tea strainers. This is because grit and muck does not get pushed into the soft bearing surfaces, as per shell bearings, so minimising the damage, but it actually abrades the bearing surfaces in Panhard engines.
If the engine was being produced today, the engine would have a disposable paper element oil filtration system. So why not your Panhard? Well it did once! If you are lucky enough to have a copy of “Revue Technique: Les Archive du Collectionneur Panhard 1954 - 1965” you will see an illustration on p.15 of a single sided oil filter, using a ‘Fram’ internal cartridge. It took its’ oil feed from the O/S upper cylinder banjo via an extended screw and returned by gravity to the oil breather/filler block. Also on p. 7, fig 10 is an oil pump mesh, that looks a bit more substantial than the 17’s tea strainer. So how does this relate to our flat twin? It says the existing oil pump can push oil up to a paper element filter, but it was not a priority as it could bypass the filter. (The other oilfeed was not filtered, nor the main oil circuit.)
In an ideal world you would start with a clean engine, the oil pump would suck up clean filtered oil and therefore no bits would score the pump faces. The clean oil would travel to the lubrication points and the “dirty” oil would return to the sump. This oil would be filtered and the cycle would continue. However most cars are not filtered this way, they have a mesh covering a pick up pipe and the oil pump pushes strained dirty oil through the filter. The cleaned oil is then fed to the lubrication points and returns to the sump. Forced filtration is used because as the filter traps material, the pressure required to pass through it increases and the flow rate falls. To compensate for this a bypass valve is fitted which opens at a preset pressure and lets a mixture of strained & filtered oil through. The need for longer service intervals on modern cars has increased their filters’ capacity and with their high flow rates there now exists an extrapolated life for filters on the suction side, assuming they have a lower flow requirement. Flat twin Panhards have low flow rates and as the engine design does not permit a cost effective break into the output of the pump, some other solution is needed, a filter on the suction side!
At the January meeting at the Brooks’ residence, just outside sunny Kendal, I showed a few people my thoughts. The basic idea consisted of four parts, a pump base adaptor, a threaded insert, a revised sump plate and a screw on oil filter cartridge. A few were enthusiastic, some not, but despite the negative comments, I felt I had to develop the idea further if only for myself and a few others! I commissioned a prototype from a precision engineer’s, and I acquired this just before the National Motorcycle Museum meeting. I fixed the bits to a dusty old crankcase and via Adrian’s PL17 we wafted along to the museum. It has been a long time since I have been motoring in a Panhard and it was thoroughly enjoyable. I do not recall as many people gawking at the car whilst I was driving so many years ago. I showed most of the people there the crankcase with the cartridge attached, and some more points were raised. George Pearsall pointed out that periodic cleaning of the slingers was void, assuming they were clean to start off with! Roger Caunt suggested you could extend the oil changes by just changing the filter. I also mentioned the likely cost for the first ten would be, £55 +p&p exc filter. This is not an unreasonable sum considering the materials, machining and assembly costs.
Concerned that this is an untried product? I have spoken to various filter companies via their Technical departments to establish critical information and viability. Generally filters’ have a service interval of 10,000 miles, and up to 5 times the oil flowing through them than our cars can deliver. If you are draining into a sump, an anti drain valve is not necessary, but most have them. If you are using the suction side of the pump, the bypass valve will be too strong, but the filter’s state will be safely monitored by the oil light illumination.
Non destructive bench test of oil pump output. So I put a bare crankcase & oil pump in an engine stand. This was not a new pump just one that was within wear limits and probably similar to yours! After blocking off the surplus oilways, I fitted the new adaptor assembly. This would allow me to assess the oil pump flow and pressure. I used a low cost 20/50W Multigrade, as most people should be using better quality oil and I needed worst case figures. Forty years ago BP Viscostatic was Panhard’s choice. I also needed to check the pressure relief valve operation so I unscrewed the core plugs in the sump and put a mini Maglite inside to illuminate the baseplate. I carried out a series of tests over two days, which allowed me to tweak the performance of the kit, and also gave me comparative data for the original equipment. The new baseplate and filter were designed to better the factory baseplate and mesh set up, but the final figures surprised me, and fitting this kit to your Panhard will put more oil into the critical bronze valve gear and crankshaft areas. This data implied that using the test filter and adaptor on a vehicle would not harm it, and the nearest was Ted Bemand’s Dyna.
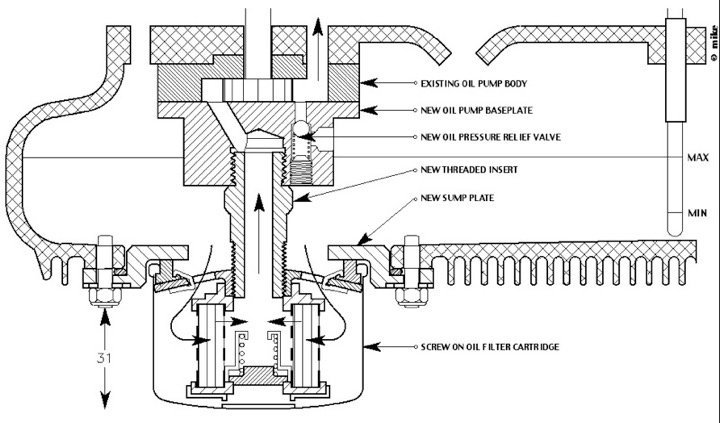
Fitting the adaptor. On arriving at Ted’s, I ran through the adaptor, the test data, and promptly fitted the kit. It took less than half an hour, and after jacking up the front of the car, for some forearm clearance, it only involved the following:
1. Drain oil and disable ignition circuit.
2. Remove six M6 nuts, existing sump plate and clean old gasket off crankcase flange.
3. Remove oil strainer by undoing the M6 nut.
4. Remove the four oil pump baseplate nuts and only remove oil pump baseplate.
5. Fit new aluminium baseplate and affix using the four M6 locknuts & washers provide
6. Double check old crankcase face is clean and ‘O’ ring is located in the groove on the new sump plate. Offer up to crankcase , fit six M6 washers and locknuts. Tighten until sump plate is seated. ‘O’ ring is a flange seal and it’s oil tight with 3 fixings!
7. Screw oil filter onto protruding threaded insert & tighten as per filter instructions.
8. Fill with oil, crank engine, undo cylinder banjos, to check oil is getting to valves.
9. Refit plugs and leads et voila!.
Driving down the road, with the untested smaller Mann/Hummel filter fitted, everything seemed to be OK, but to be honest, after a bit of 100 kph sustained motorway work, when Ted lifted off as we pulled onto the slip road, the oil light flickered! To cut a few hours short, when the Champion filter was refitted, the same one I had used in the tests, everything was OK and Ted was doing 120 kph! The next day Ted took the car to Manchester & later Widnes, and there were no problems. The filter kit is still on Ted’s car and the Champion unit is being life tested. Do not use untested filters.
The Mann filter riddle has been narrowed down to two likely causes, but I have found an even better shallower replacement, which can be modified to eliminate both. When I get the second unit, I will run comparative bench tests to check this. I can then upgrade this model to study actual oil flows & pressures inside the engine. Oil movements at idle speeds with the factory set up are now being investigated. I will have a full report, including the previous test data and schematics, in the next newsletter. For those of you who managed to get to the NEC show, I will have the latest prototype & filter on hand, and doubtless bored you silly with facts and figures! Sorry if this was the case.
Meantime any takers, as I need a ten firm orders to start. The next ones will cost more! I have put serious time, thought and money into this project and to date have sourced and bought insert stock, springs, balls, ‘O’ rings ,fasteners, and several sample filters! Any questions or enquiries to,
Mike Crane
12 April 1998
PS I didn't get 10 starters, so I took a chance, and a visit to Holland soon got things rolling
Why bother you might ask? In the last fifteen years I have been tinkering with air filtration, valve gear modifications, all things Fiat 124 Spider, Fiat twin cam and four stroke motorcycle engines. Researching and rebuilding when required and with respect to lubrication, engines with roller bearing crankshafts & big ends have real oil filtration not tea strainers. This is because grit and muck does not get pushed into the soft bearing surfaces, as per shell bearings, so minimising the damage, but it actually abrades the bearing surfaces in Panhard engines.
If the engine was being produced today, the engine would have a disposable paper element oil filtration system. So why not your Panhard? Well it did once! If you are lucky enough to have a copy of “Revue Technique: Les Archive du Collectionneur Panhard 1954 - 1965” you will see an illustration on p.15 of a single sided oil filter, using a ‘Fram’ internal cartridge. It took its’ oil feed from the O/S upper cylinder banjo via an extended screw and returned by gravity to the oil breather/filler block. Also on p. 7, fig 10 is an oil pump mesh, that looks a bit more substantial than the 17’s tea strainer. So how does this relate to our flat twin? It says the existing oil pump can push oil up to a paper element filter, but it was not a priority as it could bypass the filter. (The other oilfeed was not filtered, nor the main oil circuit.)
In an ideal world you would start with a clean engine, the oil pump would suck up clean filtered oil and therefore no bits would score the pump faces. The clean oil would travel to the lubrication points and the “dirty” oil would return to the sump. This oil would be filtered and the cycle would continue. However most cars are not filtered this way, they have a mesh covering a pick up pipe and the oil pump pushes strained dirty oil through the filter. The cleaned oil is then fed to the lubrication points and returns to the sump. Forced filtration is used because as the filter traps material, the pressure required to pass through it increases and the flow rate falls. To compensate for this a bypass valve is fitted which opens at a preset pressure and lets a mixture of strained & filtered oil through. The need for longer service intervals on modern cars has increased their filters’ capacity and with their high flow rates there now exists an extrapolated life for filters on the suction side, assuming they have a lower flow requirement. Flat twin Panhards have low flow rates and as the engine design does not permit a cost effective break into the output of the pump, some other solution is needed, a filter on the suction side!
At the January meeting at the Brooks’ residence, just outside sunny Kendal, I showed a few people my thoughts. The basic idea consisted of four parts, a pump base adaptor, a threaded insert, a revised sump plate and a screw on oil filter cartridge. A few were enthusiastic, some not, but despite the negative comments, I felt I had to develop the idea further if only for myself and a few others! I commissioned a prototype from a precision engineer’s, and I acquired this just before the National Motorcycle Museum meeting. I fixed the bits to a dusty old crankcase and via Adrian’s PL17 we wafted along to the museum. It has been a long time since I have been motoring in a Panhard and it was thoroughly enjoyable. I do not recall as many people gawking at the car whilst I was driving so many years ago. I showed most of the people there the crankcase with the cartridge attached, and some more points were raised. George Pearsall pointed out that periodic cleaning of the slingers was void, assuming they were clean to start off with! Roger Caunt suggested you could extend the oil changes by just changing the filter. I also mentioned the likely cost for the first ten would be, £55 +p&p exc filter. This is not an unreasonable sum considering the materials, machining and assembly costs.
Concerned that this is an untried product? I have spoken to various filter companies via their Technical departments to establish critical information and viability. Generally filters’ have a service interval of 10,000 miles, and up to 5 times the oil flowing through them than our cars can deliver. If you are draining into a sump, an anti drain valve is not necessary, but most have them. If you are using the suction side of the pump, the bypass valve will be too strong, but the filter’s state will be safely monitored by the oil light illumination.
Non destructive bench test of oil pump output. So I put a bare crankcase & oil pump in an engine stand. This was not a new pump just one that was within wear limits and probably similar to yours! After blocking off the surplus oilways, I fitted the new adaptor assembly. This would allow me to assess the oil pump flow and pressure. I used a low cost 20/50W Multigrade, as most people should be using better quality oil and I needed worst case figures. Forty years ago BP Viscostatic was Panhard’s choice. I also needed to check the pressure relief valve operation so I unscrewed the core plugs in the sump and put a mini Maglite inside to illuminate the baseplate. I carried out a series of tests over two days, which allowed me to tweak the performance of the kit, and also gave me comparative data for the original equipment. The new baseplate and filter were designed to better the factory baseplate and mesh set up, but the final figures surprised me, and fitting this kit to your Panhard will put more oil into the critical bronze valve gear and crankshaft areas. This data implied that using the test filter and adaptor on a vehicle would not harm it, and the nearest was Ted Bemand’s Dyna.
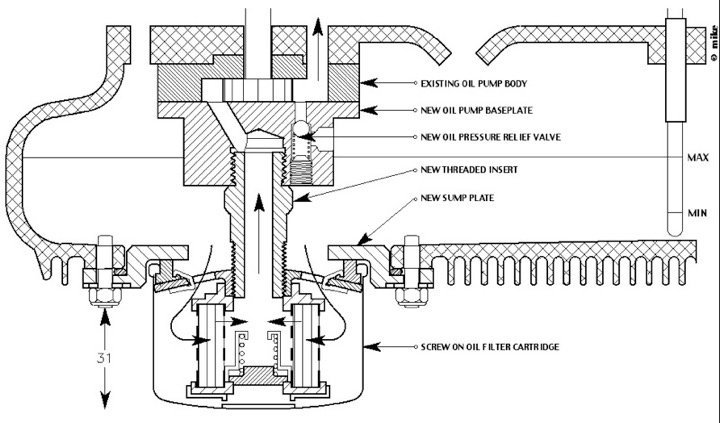
Fitting the adaptor. On arriving at Ted’s, I ran through the adaptor, the test data, and promptly fitted the kit. It took less than half an hour, and after jacking up the front of the car, for some forearm clearance, it only involved the following:
1. Drain oil and disable ignition circuit.
2. Remove six M6 nuts, existing sump plate and clean old gasket off crankcase flange.
3. Remove oil strainer by undoing the M6 nut.
4. Remove the four oil pump baseplate nuts and only remove oil pump baseplate.
5. Fit new aluminium baseplate and affix using the four M6 locknuts & washers provide
6. Double check old crankcase face is clean and ‘O’ ring is located in the groove on the new sump plate. Offer up to crankcase , fit six M6 washers and locknuts. Tighten until sump plate is seated. ‘O’ ring is a flange seal and it’s oil tight with 3 fixings!
7. Screw oil filter onto protruding threaded insert & tighten as per filter instructions.
8. Fill with oil, crank engine, undo cylinder banjos, to check oil is getting to valves.
9. Refit plugs and leads et voila!.
Driving down the road, with the untested smaller Mann/Hummel filter fitted, everything seemed to be OK, but to be honest, after a bit of 100 kph sustained motorway work, when Ted lifted off as we pulled onto the slip road, the oil light flickered! To cut a few hours short, when the Champion filter was refitted, the same one I had used in the tests, everything was OK and Ted was doing 120 kph! The next day Ted took the car to Manchester & later Widnes, and there were no problems. The filter kit is still on Ted’s car and the Champion unit is being life tested. Do not use untested filters.
The Mann filter riddle has been narrowed down to two likely causes, but I have found an even better shallower replacement, which can be modified to eliminate both. When I get the second unit, I will run comparative bench tests to check this. I can then upgrade this model to study actual oil flows & pressures inside the engine. Oil movements at idle speeds with the factory set up are now being investigated. I will have a full report, including the previous test data and schematics, in the next newsletter. For those of you who managed to get to the NEC show, I will have the latest prototype & filter on hand, and doubtless bored you silly with facts and figures! Sorry if this was the case.
Meantime any takers, as I need a ten firm orders to start. The next ones will cost more! I have put serious time, thought and money into this project and to date have sourced and bought insert stock, springs, balls, ‘O’ rings ,fasteners, and several sample filters! Any questions or enquiries to,
Mike Crane
12 April 1998
PS I didn't get 10 starters, so I took a chance, and a visit to Holland soon got things rolling
blog comments powered by Disqus