Panhard pistons and a redesign
11/03/12 21:16
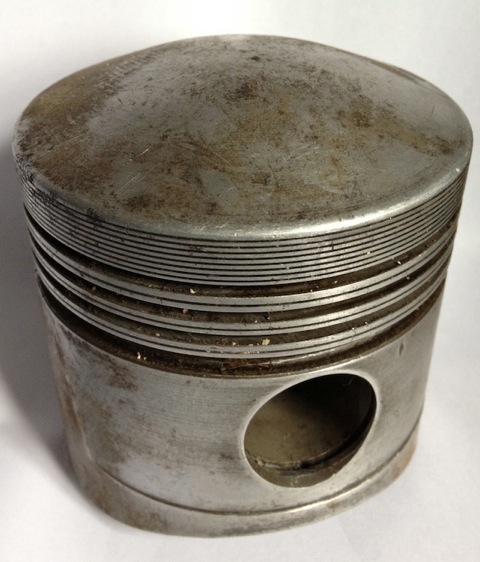
Panhard pistons are quite heavy and bulky items compared to todays’ equivalents, examples shown below, but that’s because the piston has to be domed to make the compression high enough due to their hemispherical combustion chamber layout, whereas modern day pistons have minimal surface areas applied to the piston and combustion volumes, thinner rings and latterly thermal coatings, which allow for even thinner sections.
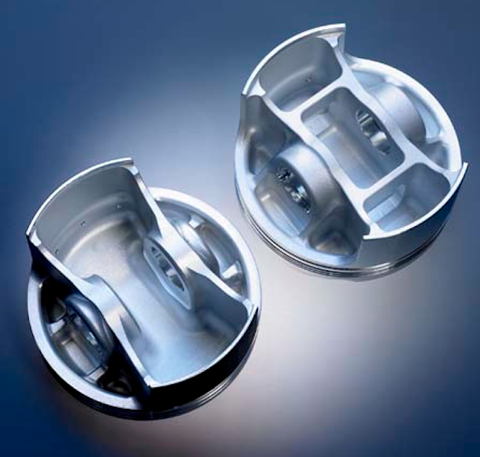
The biggest limiting factor is the close proximity of the top ring to the end of the steel liner, and as shown below the top ring is quite far down the piston, around 10mm from the top deck.
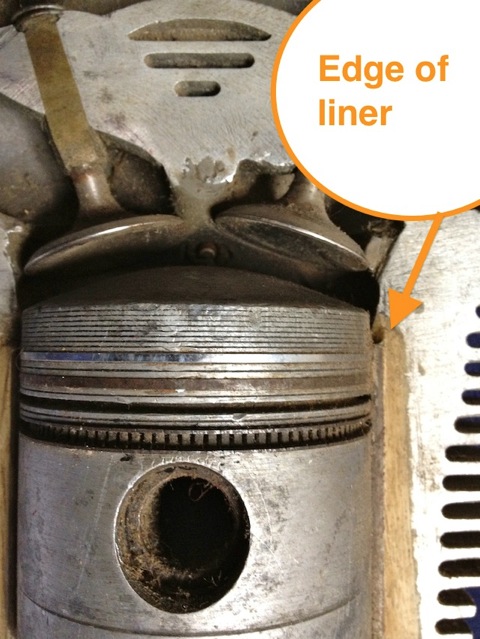
These engines are from the junk pile, but they still have their uses, as this piston was cut up to show the typical cross-sectional areas that exist within the original. There are more than one type of Panhard piston used in the flat twin engine, but this is the later 4 ringed type, that was cut up today.
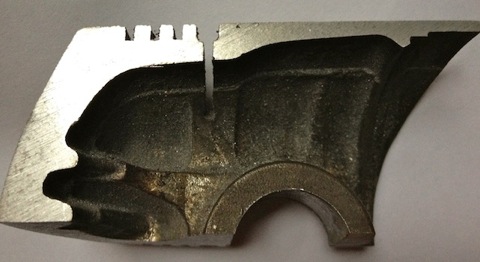
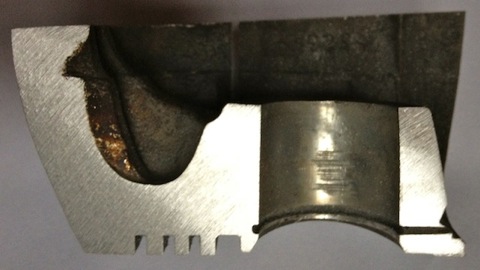
Why is this done? I need to understand why the naked Panhard piston weighs 505 grams, when my target weight for a heavily domed piston is sub 400grams, which is double the weight of a single cylinder Supermotard piston from 2002, and probably three times heavier than a complete MotoGP piston!
PANHARD PISTON REDESIGN
I need to replace the pistons and rebore Brian’s cylinder, as this engine will represent a rejuvenated and refreshed Panhard engine using mostly OEM parts. The original pistons are only available in certain sizes, and the design of them isn’t really good practice nowadays.
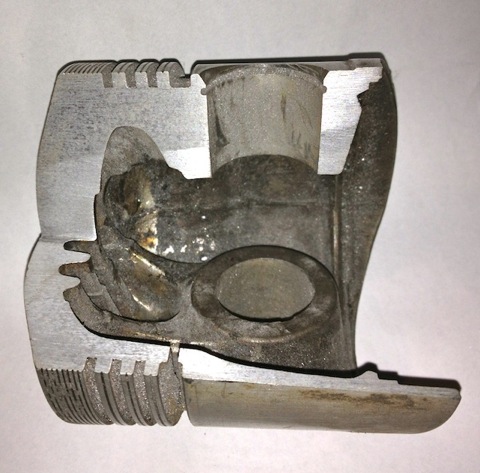
There is little that can be done about the domed area or the piston pin position, because these are factors of the combustion chamber, and also the crankcase limits using longer rods. Obviously you can shorten the cylinders, but it is a lot of work, that few people will want to pay for. Under examination, it is fair to see that the tall & shallow OEM ring construction is at odds with the more modern thin & deep thinking. The oil scraper functions have been analysed and there are several upgrade options that can be used too. Piston skirt design, and gudgeon or piston pin location strategies have all changed, as well as different materials and coating technologies, which all enhance performance or give longer life when used in marginal conditions. So ideally finding a modern day piston that would fit would seem to be the answer, but although I have known about several pistons that I can use, they all have potential issues around the top ring placement and the fixed liner.
On reflection it would be more logical to design a replacement then, but what benefits would this give?
Obviously, this will give a slight capacity increase, as you are essentially reconditioning the standard Panhard liner, which has a finite thickness, but what about the tapered bores. Hmmm, we’ll pass on this for a minute while considering other points.
Fundamentally the piston should be a lot lighter, which will reduce crankshaft loads and prolong the life of the rotating elements at higher rpms. The ring technology has changed, so these get lighter and generally use combustion pressure to effect a seal. The thinner rings also have less friction and can reduce crankcase compression blowby, but the cylinders have to be finished to a higher standard for the rings to seal correctly.
There is a possibility that an offset piston pin can be used, which reduces piston noise when the engine is warm, and more importantly reduces the shock loading on the connecting rod, by spreading the reciprocating load changes over a fractionally wider area of rotation. The slight offset or bias to the exhaust side of the piston also reduces cylinder bore wear, but this is not used in racing, because the engines are maintained more frequently, so most forged pistons don’t use this.
Lastly, there is a wealth of coatings technology that can be applied, although this does add expense to the final product, it does offer protection from nasty combustion events, and does improve reliability.
These doodles are some of my thoughts from today, and obviously I can reduce the sections some more, but the target weight of sub 400grams looks like it will be achievable now.
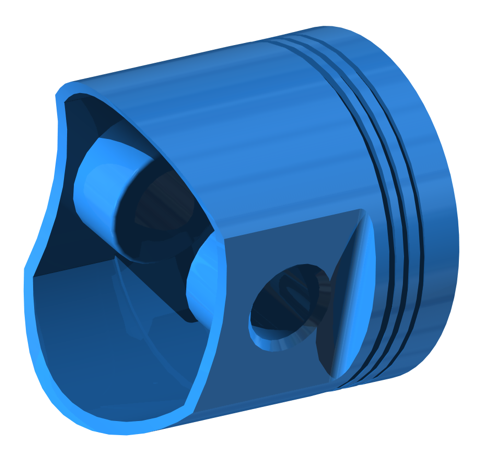
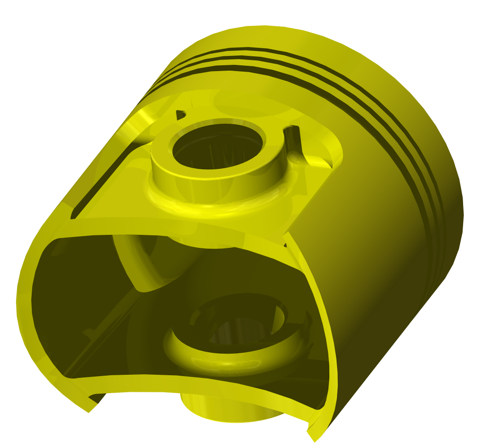
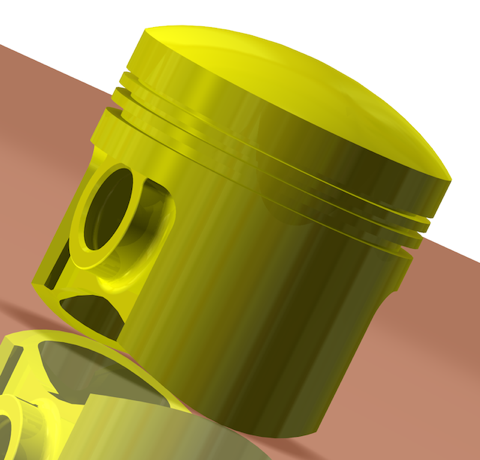
I need to do some finite element stress analysis to take it further, but hopefully those following this will understand the direction the engine is taking.
PS The tapered bores will be for another blog post.