Panhard crankcase front oil drilling reinstated
04/03/12 15:09
Next up to bring Brian’s engine up to date with the oil supply modifications is restoring the earlier oil supply method, but this time bypass all the negatives.
The later engines didn’t have this option, as can be seen here.
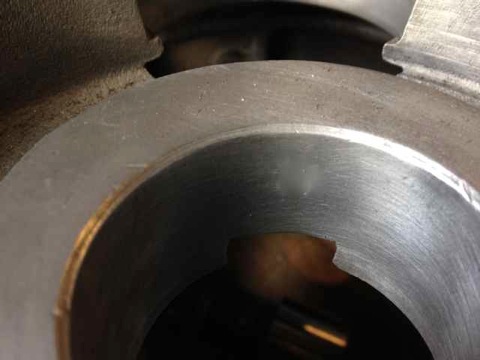
The original engines had this oil feed visible above the camshaft bore at the very front of the crankcase, which is shown below. As the camshaft rotates this drilling is filled two times per camshaft revolution, and after this it passes underneath the bearing and jumps into the slingers. Some oil splashes back and passes through the main bearing, but the rest is accelerated by the slingers on the crank web, and passes through the big end bearing before exiting and splash lubricating the little end.
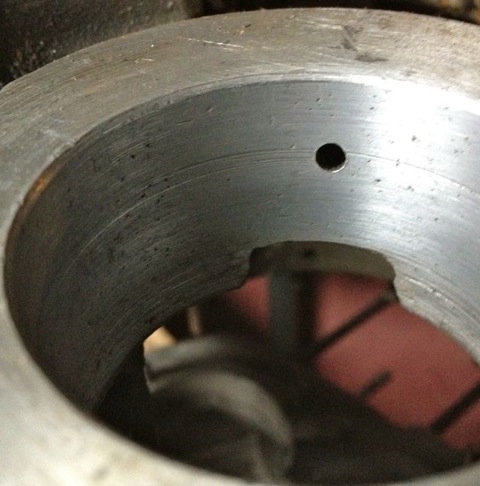
Unfortunately this hole is too small, and it led to a 50% reduction in flow rate over the rear, which is why I mod the front like so.
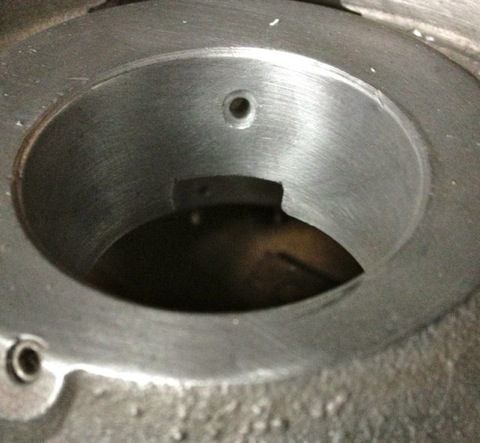
It might not be obviously apparent from the pictures, but the hole size is now 6mm diameter, whereas the one above is just 4mm. This new oil feed now matches the camshaft aperture, so that all openings, front and rear are timed equally at the rotating surfaces. The 4mm diameter hole of the earlier design will have to be enlarged to 5mm, as the rear oil feed is actually 5mm in diameter internally, but at first it is more important to get the hole in the right position, and work from this.
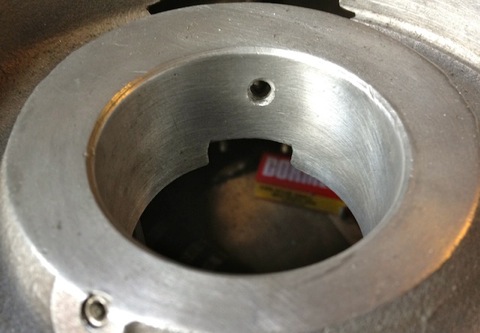
The internal oil feed pictured above now opened up to 5mm diameter, which is 50% bigger than the OEM drilling on the earlier engines. This new size matches that of the original rear bearing feed, which should equalise the flow rates. Next up, modifying the aluminium rear main bearing support casting to take a double lipped oil seal.
The later engines didn’t have this option, as can be seen here.
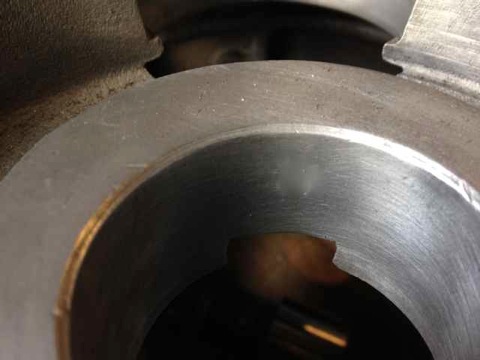
The original engines had this oil feed visible above the camshaft bore at the very front of the crankcase, which is shown below. As the camshaft rotates this drilling is filled two times per camshaft revolution, and after this it passes underneath the bearing and jumps into the slingers. Some oil splashes back and passes through the main bearing, but the rest is accelerated by the slingers on the crank web, and passes through the big end bearing before exiting and splash lubricating the little end.
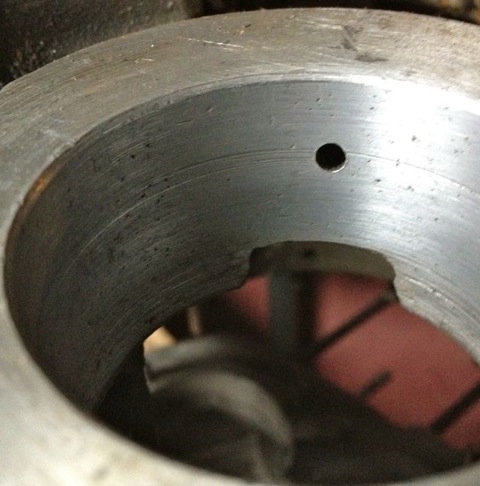
Unfortunately this hole is too small, and it led to a 50% reduction in flow rate over the rear, which is why I mod the front like so.
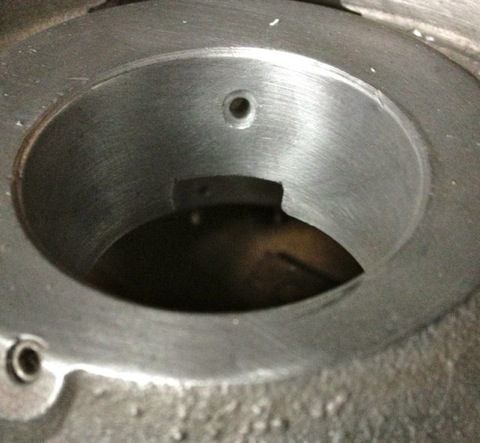
It might not be obviously apparent from the pictures, but the hole size is now 6mm diameter, whereas the one above is just 4mm. This new oil feed now matches the camshaft aperture, so that all openings, front and rear are timed equally at the rotating surfaces. The 4mm diameter hole of the earlier design will have to be enlarged to 5mm, as the rear oil feed is actually 5mm in diameter internally, but at first it is more important to get the hole in the right position, and work from this.
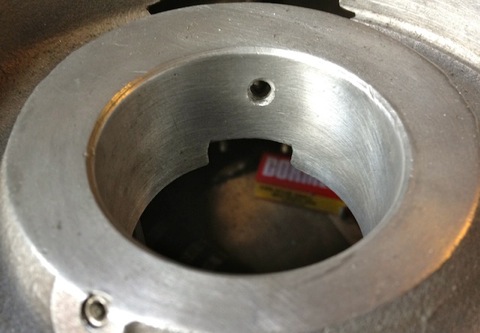
The internal oil feed pictured above now opened up to 5mm diameter, which is 50% bigger than the OEM drilling on the earlier engines. This new size matches that of the original rear bearing feed, which should equalise the flow rates. Next up, modifying the aluminium rear main bearing support casting to take a double lipped oil seal.