Panhard pistons - order placed
Saturday 24 March 2012
Over the last week, I managed to speak to the piston people, and what an engaging process that was. I started with a set idea in my head, and I really thought I knew what I wanted and then due to the limitations of the top ring to sleeve distance, the high compression or deck height of the standard set and the need for simplicity in installation, I had to go a different route.
As I discussed earlier, you can make anything work, but I wanted to avoid this. Pistons can be made in three ways, casting, forging and CNC from solid, but there are cost and number implications along the way. There are insufficient numbers to make a casting, and CNC from solid is double the expense of a machined forging, because it spends more time in the CNC machine, and has higher CAD/CAM costs. So that leaves forging and machining as the most suitable choice, but only if you can use an existing forging.
Panhard engines belong to an older generation of engine design, because nowadays you look to minimise surface areas in pistons and combustion chambers, which means domed pistons and hemispherical chambers are out. The implications for the forgings blanks are that most modern engine pistons do not have the large compression heights, and the top ring to compression height is minimised to reduce detonation, so the forgings are too small. The other thing is the bore size is slightly unusual, so you are generally looking at imperial forgings if you want to reuse the same liners.
The closest possible match to the Panhard piston on paper is a Royal Enfield Bullet piston, and that is what I thought I would be using, but it wasn’t after talking to the piston guru. I knew it was too heavy at over 600g complete, and so didn’t meet the weight targets, but I thought a little tweak here and there would sort that. It turns out it is unsuitable with the Panhard liner, and although it is good enough for a Royal Enfield, it isn’t for us.
It turns out when you look for a suitable forging, you look at the inside not the outside first, because if you want an intrinsically good design and therefore light as possible, the inner forging profile must match or follow the outer profile requirements closely, and believe it or not the original cast Panhard piston does this already. Now the selection is starting to get more focussed, so all that is really needed is a suitable forging with a domed inner profile, and enough room for the top ring detail. At this point I had to leave the meeting, because the piston designer had to look at the forging blanks in the old store. When I got back, it was really fortunate the company has been in business for 40 years, and had saved examples of the 320 forgings tools they had stored, because he found several pistons he thought might be suitable.
A short discussion later, and the choices were reduced to just one, and I just needed to confirm the dimensions in an email, so that production could be started. When I got home I burretted the combustion chamber and subtracted the piston dome volume, and worked backwards to get a higher compression version. This can always be reduced by shimming, like the original system, however I’ll be using new laser cut shims to vary the compression ratio. The 2012 engine will have a higher compression ratio, to make the more modern ring design work effectively. The latter is the limiting factor for the final rebore dimension, as it will be an existing imperial oversize set that I’ll be using. Incidentally, the oil supply for the piston pin will come off the liner walls and lubricate the piston pin via the oil control ring drillings.
As it is the start of the race season there is now a 12 week lead time, instead of the listed 8 weeks, and so today I placed an order for 12 pistons, which is six sets. This is a special developmental batch and it has a one off early adopter price, but the next batch will cost more at around £350 a set. There will need to be a piston pin or gudgeon pin conversion bush made to fit the standard rod, which varies anyway depending on the engine, that will add a little more cost to the total required. Any standard cylinder liners can be reused as they are over bored to a new controlled size. The pistons are expected to be available around the 18 June 2012. More details and pictures to be added later, but the piston is similar to this, without the valve pockets and with a smaller pin diameter.
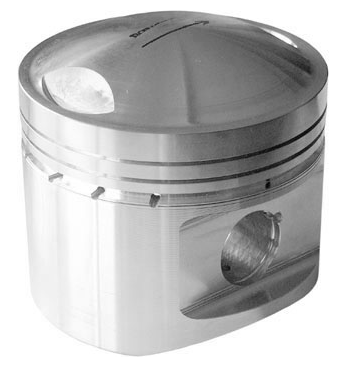
There is no doubt in my mind, over the next few batches a truly modern Panhard piston will be developed. One of the most important elements for me, is the company will continually refine the design when they receive used examples by modifying the machining incrementally. This will reduce the wear characteristics, and allows for smaller piston to cylinder liner clearances to be used and also maintain the correct clearances when hot, which brings further improvements, but the piston becomes tailored to the engine combustion processes.
This fits in with my philosophy of creating a remanufactured standard engine, that incorporates modern thinking, increases reliability, and as an added bonus, additional performance improvement too. As this work involves an engine rebuild, it would be foolish not to incorporate the other benefits I have found over the years, and this fits well with a staged development program.
Obviously this depends on what the car is being used for and/or the individual views of the owner, and it’s basically a debate about keeping original no matter what, or improving on originality, so that it can be used today. Whatever your views, or standpoint the Panhard engine is not reliable by modern day standards, and is a ticking time bomb if you own one without knowing its’ condition. For people that use their cars, you must as a general rule, no matter what side of the fence you sit...
1. Improve the oil capacity and filtration, and protect what you have.
2. Look at the crankshaft sometime, preferably rebuild it using the Peter Breed system, but definitely reduce the original crankshaft loadings by fitting lightweight pistons.
3. If you fit lightweight pistons, you should get the cylinder induction ported to reduce reversion, which counteracts the original fuelling variations and makes for smoother everyday running. I would also recommend an annealed copper gasket at the inlet manifold joint aka Peter Breed.
4. Improve the ignition timing, by fitting a modern full electronic ignition system and twin plug the head. This will improve starting, the main ignition events, and reduce the likelihood of marginal combustion triggering pinking, detonation or worst case holed pistons.
It is no coincidence that I am developing products to fit these stages, and the pistons are first to be announced as they have the longest lead time. All will be seen on the 2012 engine, which although it will look like a standard engine to most eyes, it will be totally re-engineered under the skin for use in modern day traffic (including the annual bash around Monthléry).
As I discussed earlier, you can make anything work, but I wanted to avoid this. Pistons can be made in three ways, casting, forging and CNC from solid, but there are cost and number implications along the way. There are insufficient numbers to make a casting, and CNC from solid is double the expense of a machined forging, because it spends more time in the CNC machine, and has higher CAD/CAM costs. So that leaves forging and machining as the most suitable choice, but only if you can use an existing forging.
Panhard engines belong to an older generation of engine design, because nowadays you look to minimise surface areas in pistons and combustion chambers, which means domed pistons and hemispherical chambers are out. The implications for the forgings blanks are that most modern engine pistons do not have the large compression heights, and the top ring to compression height is minimised to reduce detonation, so the forgings are too small. The other thing is the bore size is slightly unusual, so you are generally looking at imperial forgings if you want to reuse the same liners.
The closest possible match to the Panhard piston on paper is a Royal Enfield Bullet piston, and that is what I thought I would be using, but it wasn’t after talking to the piston guru. I knew it was too heavy at over 600g complete, and so didn’t meet the weight targets, but I thought a little tweak here and there would sort that. It turns out it is unsuitable with the Panhard liner, and although it is good enough for a Royal Enfield, it isn’t for us.
It turns out when you look for a suitable forging, you look at the inside not the outside first, because if you want an intrinsically good design and therefore light as possible, the inner forging profile must match or follow the outer profile requirements closely, and believe it or not the original cast Panhard piston does this already. Now the selection is starting to get more focussed, so all that is really needed is a suitable forging with a domed inner profile, and enough room for the top ring detail. At this point I had to leave the meeting, because the piston designer had to look at the forging blanks in the old store. When I got back, it was really fortunate the company has been in business for 40 years, and had saved examples of the 320 forgings tools they had stored, because he found several pistons he thought might be suitable.
A short discussion later, and the choices were reduced to just one, and I just needed to confirm the dimensions in an email, so that production could be started. When I got home I burretted the combustion chamber and subtracted the piston dome volume, and worked backwards to get a higher compression version. This can always be reduced by shimming, like the original system, however I’ll be using new laser cut shims to vary the compression ratio. The 2012 engine will have a higher compression ratio, to make the more modern ring design work effectively. The latter is the limiting factor for the final rebore dimension, as it will be an existing imperial oversize set that I’ll be using. Incidentally, the oil supply for the piston pin will come off the liner walls and lubricate the piston pin via the oil control ring drillings.
As it is the start of the race season there is now a 12 week lead time, instead of the listed 8 weeks, and so today I placed an order for 12 pistons, which is six sets. This is a special developmental batch and it has a one off early adopter price, but the next batch will cost more at around £350 a set. There will need to be a piston pin or gudgeon pin conversion bush made to fit the standard rod, which varies anyway depending on the engine, that will add a little more cost to the total required. Any standard cylinder liners can be reused as they are over bored to a new controlled size. The pistons are expected to be available around the 18 June 2012. More details and pictures to be added later, but the piston is similar to this, without the valve pockets and with a smaller pin diameter.
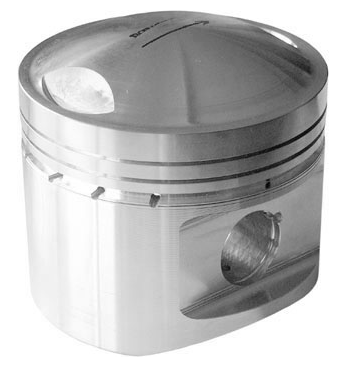
There is no doubt in my mind, over the next few batches a truly modern Panhard piston will be developed. One of the most important elements for me, is the company will continually refine the design when they receive used examples by modifying the machining incrementally. This will reduce the wear characteristics, and allows for smaller piston to cylinder liner clearances to be used and also maintain the correct clearances when hot, which brings further improvements, but the piston becomes tailored to the engine combustion processes.
This fits in with my philosophy of creating a remanufactured standard engine, that incorporates modern thinking, increases reliability, and as an added bonus, additional performance improvement too. As this work involves an engine rebuild, it would be foolish not to incorporate the other benefits I have found over the years, and this fits well with a staged development program.
Obviously this depends on what the car is being used for and/or the individual views of the owner, and it’s basically a debate about keeping original no matter what, or improving on originality, so that it can be used today. Whatever your views, or standpoint the Panhard engine is not reliable by modern day standards, and is a ticking time bomb if you own one without knowing its’ condition. For people that use their cars, you must as a general rule, no matter what side of the fence you sit...
1. Improve the oil capacity and filtration, and protect what you have.
2. Look at the crankshaft sometime, preferably rebuild it using the Peter Breed system, but definitely reduce the original crankshaft loadings by fitting lightweight pistons.
3. If you fit lightweight pistons, you should get the cylinder induction ported to reduce reversion, which counteracts the original fuelling variations and makes for smoother everyday running. I would also recommend an annealed copper gasket at the inlet manifold joint aka Peter Breed.
4. Improve the ignition timing, by fitting a modern full electronic ignition system and twin plug the head. This will improve starting, the main ignition events, and reduce the likelihood of marginal combustion triggering pinking, detonation or worst case holed pistons.
It is no coincidence that I am developing products to fit these stages, and the pistons are first to be announced as they have the longest lead time. All will be seen on the 2012 engine, which although it will look like a standard engine to most eyes, it will be totally re-engineered under the skin for use in modern day traffic (including the annual bash around Monthléry).