Panhard engine stand
Thursday 30 June 2011
A long time ago I needed to test my Panhard engines, and as I didn’t have a car on the road, an engine dyno would have been the next best thing. However finding one is another story, so I did the next best thing, found a roller dyno and thought about making an engine frame that’ll drive it. I was lucky there was an inertial dyno about two miles from me, but I never did get chance to make the “motorised wheelbarrow” that would bolt to it, as I put the engine in a Panhard PL17 and it worked so well, that it was obvious at the time there were improvements, so the need to construct something fell by the wayside.
Fast forward several years later, fuel injection projects on my motorcycle engines, FZR1000, GTS1000 & YZF1000, mean an engine dyno is an essential requirement to do this work properly. As I won’t be putting a Panhard on the road short term, and I’d like to benchmark these engines too, so it makes sense to revisit the engine dyno project again, but allow for & consider both these options at the same time.
The bike engine is straightforward as it is chain driven, but the Panhard isn’t, so I’d have to convert the flywheel to accept chain drive, as you can see in the picture below. This is the unfinished raw metal version complete with a dummy engine, which is a partial crankcase and a split cylinder & head from another project. I needed to make sure the engine support plate cleared the inlet manifold stubs, which it does now.
The engine frame is not fastened to the wheel subframe when the picture was taken, and neither is the sprocket is, as I am trying to keep the chain tension and length the same for any combo of engine rig I use, and I need to keep disassembling the stand and fitting other parts. If I can keep the same chain, it will simplify the swap over process, and so make the installation of other engines easier. Additionally, I am going to convert this into a freestanding engine stand, so I need to make a simple rear support frame, which will probably be a folding structure, probably like an ironing board stand, that tucks out of the way as I slide the engine rig onto the wheel rig. This means I can do basic run tests without the dyne, and free up dyne room for other projects.
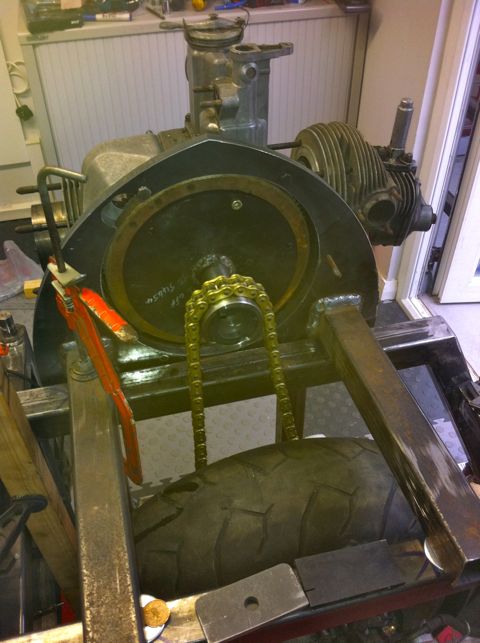
In the latest pic, everything seems to check out, as I now have a virtually complete engine fitted. It looks like I don’t need any extra brackets welding to the frame other than a battery support & the associated control panel shelf, so I will be sending it off to the powder coaters soon. Alternator conversion was a previous modification that had been dormant for a few years too, and it was a nice tidy fit at the time, however it’s powered by Lucas, so that probably won’t appeal to our French cousins! However these alternators are great value for money compared to the smaller Denso units, and readily available.
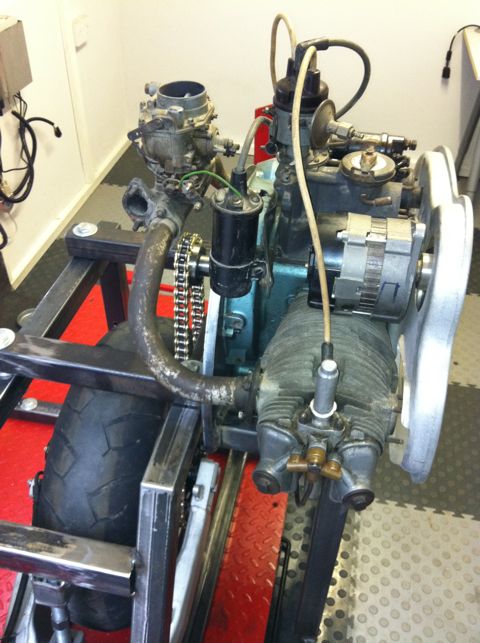
Fast forward several years later, fuel injection projects on my motorcycle engines, FZR1000, GTS1000 & YZF1000, mean an engine dyno is an essential requirement to do this work properly. As I won’t be putting a Panhard on the road short term, and I’d like to benchmark these engines too, so it makes sense to revisit the engine dyno project again, but allow for & consider both these options at the same time.
The bike engine is straightforward as it is chain driven, but the Panhard isn’t, so I’d have to convert the flywheel to accept chain drive, as you can see in the picture below. This is the unfinished raw metal version complete with a dummy engine, which is a partial crankcase and a split cylinder & head from another project. I needed to make sure the engine support plate cleared the inlet manifold stubs, which it does now.
The engine frame is not fastened to the wheel subframe when the picture was taken, and neither is the sprocket is, as I am trying to keep the chain tension and length the same for any combo of engine rig I use, and I need to keep disassembling the stand and fitting other parts. If I can keep the same chain, it will simplify the swap over process, and so make the installation of other engines easier. Additionally, I am going to convert this into a freestanding engine stand, so I need to make a simple rear support frame, which will probably be a folding structure, probably like an ironing board stand, that tucks out of the way as I slide the engine rig onto the wheel rig. This means I can do basic run tests without the dyne, and free up dyne room for other projects.
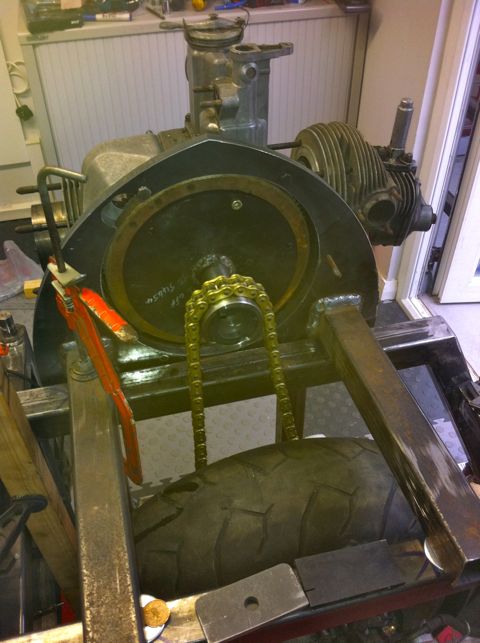
In the latest pic, everything seems to check out, as I now have a virtually complete engine fitted. It looks like I don’t need any extra brackets welding to the frame other than a battery support & the associated control panel shelf, so I will be sending it off to the powder coaters soon. Alternator conversion was a previous modification that had been dormant for a few years too, and it was a nice tidy fit at the time, however it’s powered by Lucas, so that probably won’t appeal to our French cousins! However these alternators are great value for money compared to the smaller Denso units, and readily available.
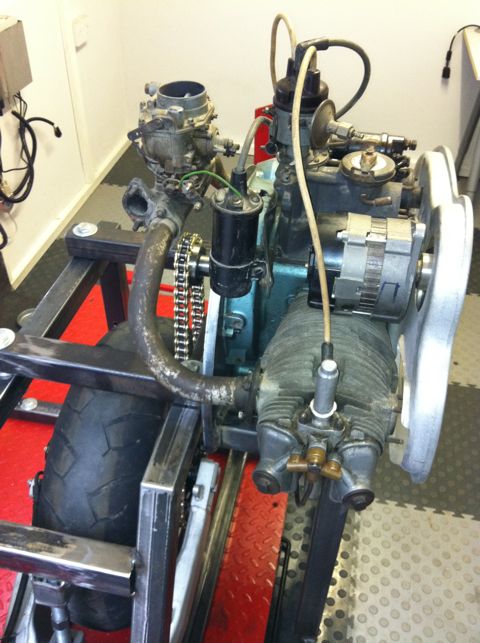